Fábrica de automóviles utiliza rádios de ProSoft Technology para ayudar a eliminar choques.
Todos hemos visto accidentes automovilísticos. La mayoría de nosotros ha tenido uno o dos en nuestras vidas, pero imagine un accidente en el que ningún coche tenga volante o ruedas de algún tipo. ¿Difícil de imaginar? No lo es si usted estuviera viendo una línea de montaje en una planta de fabricación de automóviles. No hace falta decirlo, pero hacer que los coches se estrellen antes de ser completamente ensamblados, no es bueno para el resultado final.
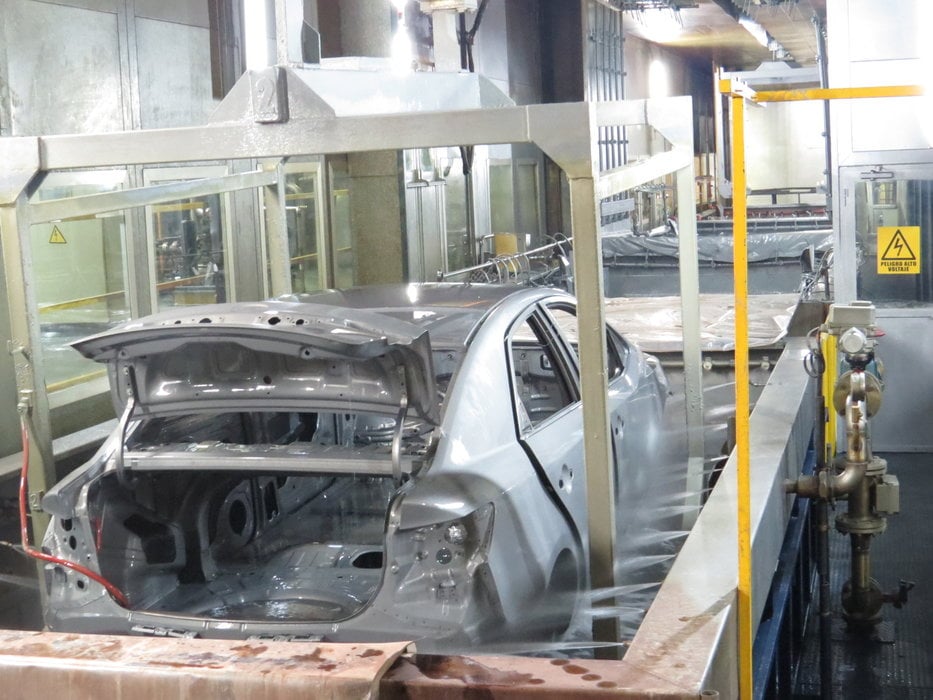
Ese era el problema que Automóviles del Ecuador S.A. (AYMESA) estaba experimentando en su planta de fabricación de Hyundai en Ecuador. AYMESA necesitaba mejorar el Sistema de Monorriel Electrificado (SME) en su taller de pintura, específicamente en el proceso de cataforesis, llamado ELPO.
La electrodeposición catódica o cataforesis, es un proceso completamente automatizado pintado por inmersión, que está basado en el movimiento de partículas cargadas en un campo eléctrico (pintura) hacia un polo cargado opuestamente (superficie metálica a ser pintada). El equipo que da la carga eléctrica en el proceso de cataforesis se llama Rectificador.
Antes de que la pintura sea aplicada, las superficies pasan por un proceso preparatorio que incluye desengrasado, fosfatado y varios enjuagues (véase figura 1). El objetivo principal del proceso de preparación y recubrimiento de fosfato es proteger las superficies de corrosión; esta técnica también permite que se pinten las áreas de difícil acceso, como áreas hundidas y tubería. Una vez que se ha aplicado la pintura, las superficies son calentadas para secar y curar.
El SME transporta portadores de carrocería alrededor de un circuito que viaja a través de los 140 metros de largo que mide el taller de pintura (véase figura 2). En la estación de carga del taller de pintura, una carrocería es cargada en un portador móvil, el cual es levantado a 5 metros del suelo y unido al SME. La carrocería se pasa a través de 12 estaciones secuenciales. En cada estación de inmersión, los portadores se detienen para permitir que dos montacargas a bordo bajen la carrocería en un baño de inmersión. Cuando el proceso es completado en una estación, los montacargas levantan la carrocería y el portador se mueve a través del monorriel a la siguiente estación.
Cada portador móvil incluye un controlador MicroLogixTM y tres Mandos de Frecuencia Variable (MFV) para operar los dos montacargas y el accionamiento de traslación de dos ruedas de fricción. Hay un controlador Maestro estacionario CompactLogixTM L35E cerca de la primera estación de carga que envía comandos a través del sistema de rieles conductor.
“Este sistema se volvió muy peligroso cuando los conductores eléctricos se rompieron, causando colisiones entre portadores móviles y un tiempo de inactividad no programado”, dijo Pablo Padilla, supervisor de mantenimiento ELPO para AYMESA.
“También, como no podíamos cambiar el voltaje especifico en el proceso de cataforesis para diferentes modelos de coches, los automóviles pequeños salían con una capa de pintura más espesa”, dijo Padilla. Esto requiere tiempo adicional para lijar y mantener nuestro parámetro de calidad.
Padilla y su jefe, Luis Olivo, gerente de Mantenimiento para AYMESA, escucharon acerca de los radios de ProSoft Technology en la conferencia Rockwell Automation© en Ecuador. “Sabíamos que ProSoft tenía una reputación sólida apoyando los controles y las interfaces de comunicación de Rockwell”, dijo Olivo.
“Queríamos aprovechar que tenemos controladores móviles a bordo para cada portador y permitir la comunicación vía Ethernet a través de una red inalámbrica de alta velocidad”, agregó Padilla.
Sin embargo, los ingenieros tenían sus dudas respecto a la confiabilidad de las redes inalámbricas en un ambiente rodeado de metal en movimiento, ya que las señales de radio se reflejan en los objetos metálicos y rebotan en todas direcciones, causando una interferencia multidireccional. El taller de pintura tiene paredes y techo de metal; los portadores son objetos masivos de metal, al igual que las carrocerías que cargan. Todas estas masas de metal en constante movimiento resultan en un ambiente de radio frecuencia siempre cambiante oportuno para interferencias de radio o corrupción en el flujo de datos..
“Los radios 802.11n de ProSoft Technology con itinerancia rápida de datos, utilizan algoritmos filtrados de alta eficacia y permiten el ajuste de la potencia emitida”, dijo Padilla. Ambas características superan los problemas de interferencia multidireccional. Además, el asesoramiento experto de ProSoft respecto a la apropiada selección y colocación de la antena fue un factor importante que contribuyó al éxito general de la aplicación.
El nuevo sistema de control consiste en un radio Maestro conectado a la red Ethernet del PLC en la que el PLC principal es una parte. Cada portador SME independiente tiene un controlador local y un radio ProSoft que actúa como repetidor para establecer la conexión inalámbrica con el controlador principal. Los seis portadores móviles se comunican entre sí aparte con el radio Maestro.
“Ya que la aplicación de este SME es de tiempo crítico, cada radio repetidor está conectado con su radio Maestro todo el tiempo para evitar retrasos de conmutación de un radio Maestro a otro, mientras los portadores están en movimiento”, dijo Padilla.
Al optar por esta red inalámbrica, AYMESA fue capaz de obtener varios beneficios:
- La implementación de un sistema de visión que consiste en una cámara para identificar el modelo del coche que entra en el taller de pintura. Esto, en conjunto con un nuevo sistema de recetas para establecer las alturas de inmersión y los tiempos de rociado de agua según el modelo del coche, redujo el tiempo de procesamiento y optimizaron el consumo de agua. El tiempo total de procesamiento por portador móvil fue reducido por tres minutos (un 6%).
- La capacidad de enviar los datos de tiempo y de voltaje al rectificador a través de la red inalámbrica. Ahora, el rectificador da una carga eléctrica específica para cada modelo de coche, eliminando el exceso de pintura en los modelos más pequeños.
- La capacidad de controlar el sistema SME en tiempo real, incrementando la confiabilidad y reduciendo el tiempo de inactividad.
- La capacidad de implementar un control remoto a través de un teclado inalámbrico con un alcance de 100 metros para controlar manualmente cada operador móvil.
- Indicación de las alarmas de cada operador móvil en el PanelViewTM en la sala de control.
- Y lo mejor de todo, las colisiones entre los portadores móviles se redujeron en 100 por ciento, ya que con la red inalámbrica, cada portador conoce su posición en relación con los demás.
www.psft.com/rlx2hyundai-es
Escrita por Danetta Bramhall
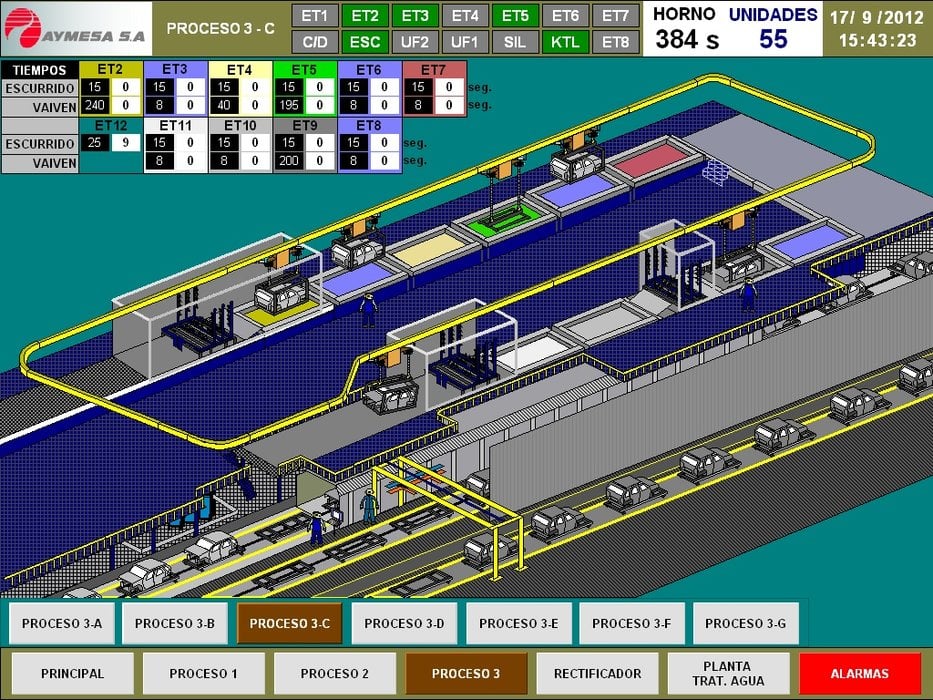