www.mexicoindustrial.net
22
'20
Written on Modified on
El camino hacia la Automatización Robótica de Procesos: Comience en pequeño, Escale a Grande
Introducir la automatización robótica en un flujo de trabajo establecido puede parecer complicado y costoso. Con la última tecnología modular y herramientas de configuración intuitivas, las compañías pueden comenzar a adquirir los beneficios de manera rápida y fácil, y escalar y actualizar sus sistemas a medida que crezca su confianza.
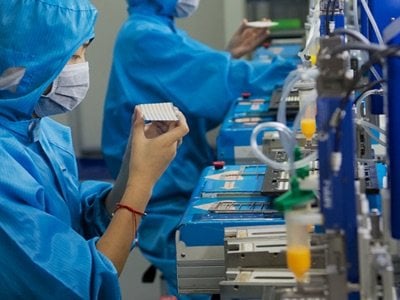
Los procesos industriales dependen cada vez más de la automatización para cumplir los objetivos de productividad, al garantizar una calidad de producto constante y un alto rendimiento. Un proceso puede estar completamente automatizado, sin intervención humana de extremo a extremo, o parcialmente automatizado combinando las fortalezas de los trabajadores humanos y las máquinas.
Imagíne humanos y máquinas cooperando en el mismo espacio, y a día de hoy, muchos probablemente imaginen una serie de robots colaborativos multi-articulados ("cobots") programados para gestionar las tareas repetitivas o físicamente exigentes, mientras sus compañeros de trabajo humanos, proporcionan la destreza manual o las aportaciones creativas necesarias para completar el proceso. Sin embargo, la introducción de cobots en una fábrica exige una importante optimización del proceso y una reorganización física del espacio de trabajo.
Automatización robótica de procesos de nivel básico
Por otro lado, las empresas fabricantes pueden comenzar a adquirir los beneficios de la automatización de procesos robóticos de una manera más simple y menos invasiva. Muchas líneas de producción son atendidas por trabajadores humanos, que realizan procesos en piezas de trabajo suministradas por una cinta transportadora. El aumento de la velocidad del transportador debería alimentar las piezas de trabajo más rápidamente y permitir una mayor productividad, pero a menudo este no es el caso. Aunque los trabajadores son físicamente capaces de seguir el ritmo del transporte más rápido, pueden surgir problemas cuando las piezas de trabajo alcanzan los topes finales a velocidades más altas y pueden desplazarse o incluso caer al suelo. La productividad puede reducirse como resultado del aumento de la velocidad del transportador.
La tecnología robóticas puede ayudar a superar este problema. Los robots lineales pueden reemplazar a los transportadores convencionales y son más fáciles de programar, con ubicaciones de inicio y detención definidas digitalmente sin necesidad de paradas finales mecánicas. La aceleración y la desaceleración ocurren sin problemas dentro de distancias predefinidas, lo que permite rápidas velocidades de tránsito. Varios de estos módulos pueden funcionar independientemente en la misma línea de producción para reemplazar un único transportador de velocidad fija e invariable. Esto brinda la flexibilidad de optimizar la velocidad de transporte en múltiples zonas a lo largo de la línea para adaptarse a los requisitos de cada proceso y equilibrar el flujo de trabajo.
Además, la flexibilidad para avanzar y retroceder abre nuevas oportunidades para lograr una eficiencia aún mayor. Yamaha ha permitido a varios clientes aprovechar estos beneficios al integrar su módulo transportador lineal robótico LCMR200 en las líneas de producción. Este modelo es rápido, eficiente y también menos exigente de reorganización del flujo de trabajo que la organización de cobots articulados de varios ejes.
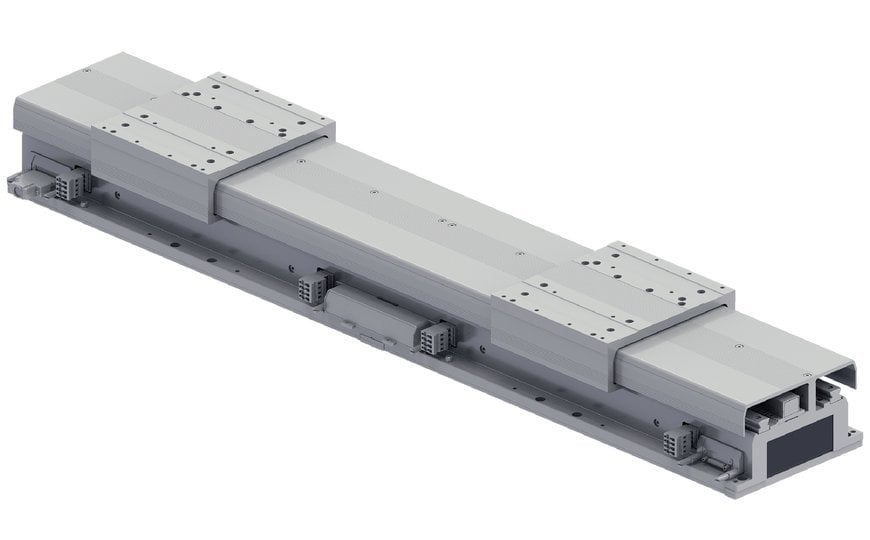
Este módulo lineal reemplaza a los transportadores convencionales, brindando velocidad y suavidad al robot.
Este robot lineal modular puede proporcionar una introducción conveniente al potencial de la automatización robótica de procesos, que puede extenderse desde el simple reemplazo de una cinta transportadora o mesa de indexación hasta la automatización completa del proceso de extremo a extremo en una celda protegida de montaje de robots.
Cuando se requiere crear un flujo de proceso automatizado robótico completo para fabricar productos pequeños como altavoces o módulos para automoción que están compuestos de varias partes, los integradores de soluciones a menudo necesitan combinar robots de varios tipos para realizar todas las acciones de ensamblaje individuales de manera rentable y en un espacio eficiente. Para ayudar, Yamaha tiene una selección única y completa de robots industriales de todos los tipos comúnmente utilizados, desde el modular LCMR200 y otros robots de un solo eje hasta cartesianos y SCARA. Estos brindan a los integradores de soluciones todas las opciones que necesitan para crear un flujo de trabajo eficiente, incluso cuando el espacio de la fábrica es escaso, a la vez que tienen en cuenta consideraciones importantes como la capacidad de mantenimiento, la capacidad de programación y la facilidad de uso.
Escalando, ahorrando espacio
Hay muchos aspectos que ahorran espacio en la línea de robots de Yamaha, como la serie de robots SCARA YK-TW de tipo órbita, montados en el techo, que permiten el movimiento de paso subterráneo permitiendo que la punta pase debajo de la unidad principal. Lograr una huella de proceso compacta puede ser extremadamente importante, por ejemplo, para los fabricantes de equipos originales (OEM) que buscan "re-apuntalar" o volver a poner bajo control interno los procesos anteriormente externalizados. Si bien los cambios económicos globales pueden significar que el re-apuntalamiento tiene sentido financiero, a menudo la fábrica local tiene muy poco espacio disponible para albergar los procesos de retorno. Donde cada centímetro cuadrado es valioso, los robots SCARA de tipo órbita han demostrado que pueden funcionar dentro de espacios increíblemente reducidos. Con una longitud de brazo de 350 mm y una capacidad de carga de 5 kg, se puede lograr un ancho de instalación de solo 492 mm.
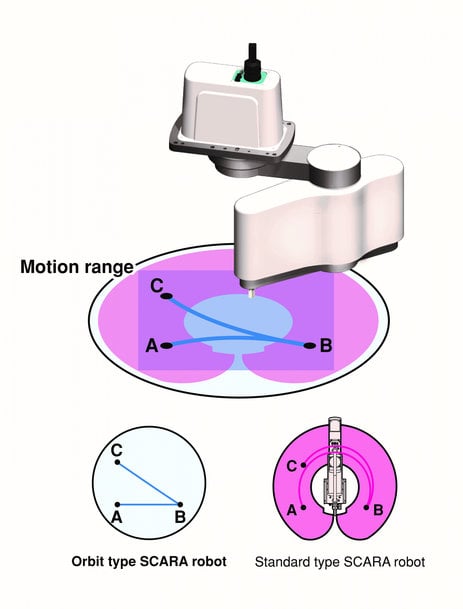
Los robots de "paso inferior" montados en el techo utilizan eficientemente el espacio del suelo de la fábrica.
Las principales fortalezas de los robots SCARA residen en recuperar y mover rápidamente las piezas de trabajo, y en realizar procesos de ensamblaje como atornillar y dispensar con precisión adhesivos, selladores o materiales de interfaz térmica. Los tamaños típicos de los robots SCARA varían desde una longitud de brazo de aproximadamente 120 mm con una capacidad de carga de aproximadamente 1 kg, hasta modelos de 1200 mm capaces de manejar hasta 50 kg. La familia YK-XG de Yamaha presenta transmisiones de correa sin mantenimiento que permiten movimientos de alta velocidad y alta precisión en cuatro ejes. Además, el momento de inercia está optimizado para permitir la rotación rápida de objetos pesados, donde las máquinas convencionales deben reducir su velocidad, lo que resulta en tiempos de contacto más largos.
Beneficiándose de una larga experiencia basada en los primeros robots industriales creados para automatizar el ensamblaje de gran volumen de piezas de motocicletas en la década de 1970, Yamaha ha podido desarrollar sus robots a un alto nivel de sofisticación con características innovadoras como el TRANSERVO que permite a los motores paso a paso ofrecer alta velocidad y alto torque.
Otras características que los integradores valoran para ayudar a simplificar los desafíos de diseño de soluciones incluyen lubricación de bajo mantenimiento y barreras contaminantes efectivas, piezas mecánicas innovadoras de alta rigidez que aseguran una precisión superior incluso bajo altas fuerzas de presión, y el uso generalizado de solucionadores de posición que son más robustos y fiables que los detectores de posición ópticos tradicionales.
Con una variedad de sistemas de control para elegir, los integradores pueden configurar una solución asequible para satisfacer el mayor desafío de automatización y al mismo tiempo dejar el camino despejado para la futura adaptabilidad y escalamiento. Las unidades de control simples para el posicionamiento básico y la conducción permiten que los robots de un solo eje se controlen fácilmente con apuntamiento coordinado o entrada de tren de pulsos, para minimizar la programación. Por otro lado, los controladores multieje pueden usarse para manejar uno o más robots de acceso simple o doble simultáneamente. Se pueden vincular hasta cuatro controladores de 4 ejes en la configuración maestro-esclavo para gestionar hasta 16 ejes y consolidar el control en un programa escrito en el lenguaje robot de Yamaha, que es una versión ampliada de BASIC.
Actualiza con confianza
El éxito en un primer proyecto de automatización a menudo alienta a los operarios a escalar o aumentar sus sistemas para una mayor productividad o calidad al final de la línea. La introducción de la visión artificial es una actualización popular, aunque la tecnología generalmente requiere conocimientos especializados y procesos de configuración tradicionales que pueden ser complicados y llevar mucho tiempo.
Yamaha se propuso facilitar la visión del robot al crear su sistema RCXiVY2+. En un sistema de visión robótico típico, las cámaras están conectadas a un procesador de visión dedicado, que luego se comunica con el controlador del sistema principal a través de un enlace de datos en serie. En el RCXiVY2+, el procesamiento de imágenes, el control de iluminación y el procesamiento de los datos de seguimiento del transportador se manejan dentro del programa del robot, utilizando instrucciones de visión dedicadas creadas por Yamaha e incorporadas al conjunto de instrucciones BASIC ampliado. El conjunto de instrucciones de visión simplifica la búsqueda y el seguimiento de componentes y reduce los tiempos de búsqueda hasta en un 50%. La búsqueda más rápida mejora la detección de piezas a altas velocidades del transportador, lo que permite una recogida mejorada y menores tiempos de contacto.
Con hardware que incluye un panel de visión con una interfaz de cámara GigE, un panel de control de iluminación y un panel de seguimiento que fácilmente se instalan directamente en el controlador de robot multieje de la serie RCX3, se evitan muchos problemas de integración y se garantiza la compatibilidad con los periféricos. Además, debido a que la visión se gestiona desde el programa del robot, no es necesario crear una rutina de conversión de coordenadas. Además, el sistema integrado de Yamaha aumenta el rendimiento al eliminar los retrasos experimentados con la visión convencional cuando los datos de la cámara pasan a través de un procesador de visión independiente y luego al controlador del robot.
Para acelerar la configuración del sistema, un proceso de calibración simple ayuda a alinear rápidamente las coordenadas de la cámara con la ayuda de un asistente, y una herramienta gráfica reduce el registro de la pieza de trabajo a tres sencillos pasos al ayudar con la captura de imágenes, el ajuste del contorno y el registro de la posición de detección. En general, el tiempo de configuración es aproximadamente un 80 por ciento más rápido que con un sistema de visión artificial convencional.
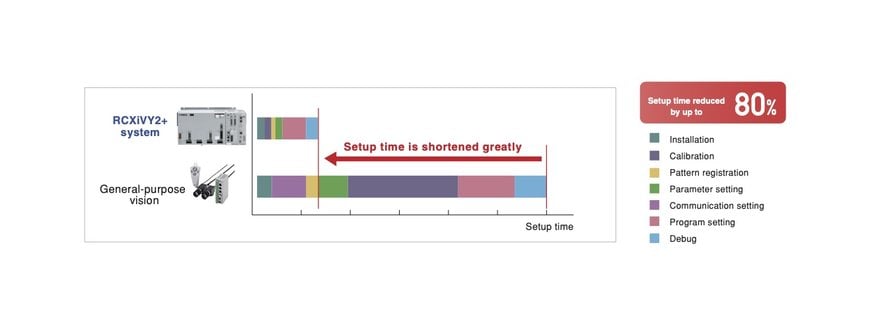
RCXiVY2 + ayuda a los usuarios a ser productivos más rápidamente
Cuando está en acción, un potente motor de búsqueda de borde de imagen mejora la detección de piezas. El sistema puede detectar tornillos y arandelas que fijan piezas, detectar elementos en un paquete o en una placa de circuito impreso, verificar agujeros perforados y contar objetos como botellas en un palet, o componentes electrónicos. La salida DVI-I de la cámara permite a los usuarios analizar el estado de búsqueda en cualquier momento y los usuarios pueden registrar hasta 254 piezas personalizadas adicionales para la detección automática. Las cámaras del RCXiVY2+ se pueden montar en ubicaciones fijas encima y / o debajo de la pieza de trabajo, o en el robot. Cuando se monta en el robot, las coordenadas de la cámara se ajustan automáticamente para corregir el movimiento.
El sistema RCXiVY2 + también introduce un nuevo enfoque para el procesamiento de imágenes conocido como "detección de manchas", que puede reconocer objetos que tienen formas irregulares hasta 10 veces más rápido que los métodos tradicionales de detección de bordes. Esto mejora la selección, el reconocimiento de presencia y el conteo a alta velocidad de múltiples piezas de trabajo, y es particularmente efectivo con artículos como alimentos y ropa, ampliando así la posible gama de aplicaciones para la visión robótica. El sistema también puede reconocer piezas superpuestas y excluirlas del objetivo de búsqueda.
Conclusión
Los procesos de ensamblaje manual convencionales, incluso cuando están asistidos por automatización básica como transportadores motorizados, ofrecen un alcance limitado para aumentar el rendimiento y la productividad. Los enfoques típicos para mejorar el tiempo de contacto a menudo pueden tener el efecto contrario en la productividad, mientras que incorporan más trabajadores y líneas de producción adicionales aumenta los costes operativos y exige más espacio en la planta de la fábrica.
Comenzar el viaje hacia la automatización de procesos robóticos puede ser fácil y no disruptivo si se aborda de la manera correcta, como al reemplazar transportadores inflexibles o tablas de indexación consumidores de espacio, con robots lineales programables. Como filas de confianza, la automatización se puede extender a otros procesos y líneas de producción, y se pueden agregar actualizaciones como la visión artificial, lo que ofrece un retorno de la inversión cada vez mayor.
www.yamaha-motor-im.de