www.mexicoindustrial.net
19
'18
Written on Modified on
Aprenda sobre herramientas mecánicas para rodamientos en la NSK academy
Cualquier persona interesada en conocer los mejores procedimientos de montaje y desmontaje de rodamientos utilizando herramientas mecánicas puede registrarse en la plataforma de formación online de la NSK academy (www.nskacademy.com) para descubrir el último tutorial del programa AIP+ (Programa de Valor Añadido). Compuesto por un curso, un vídeo y un cuestionario, los alumnos pueden abrirse camino a través del nuevo módulo de herramientas mecánicas, recibiendo un certificado al completarlo satisfactoriamente.
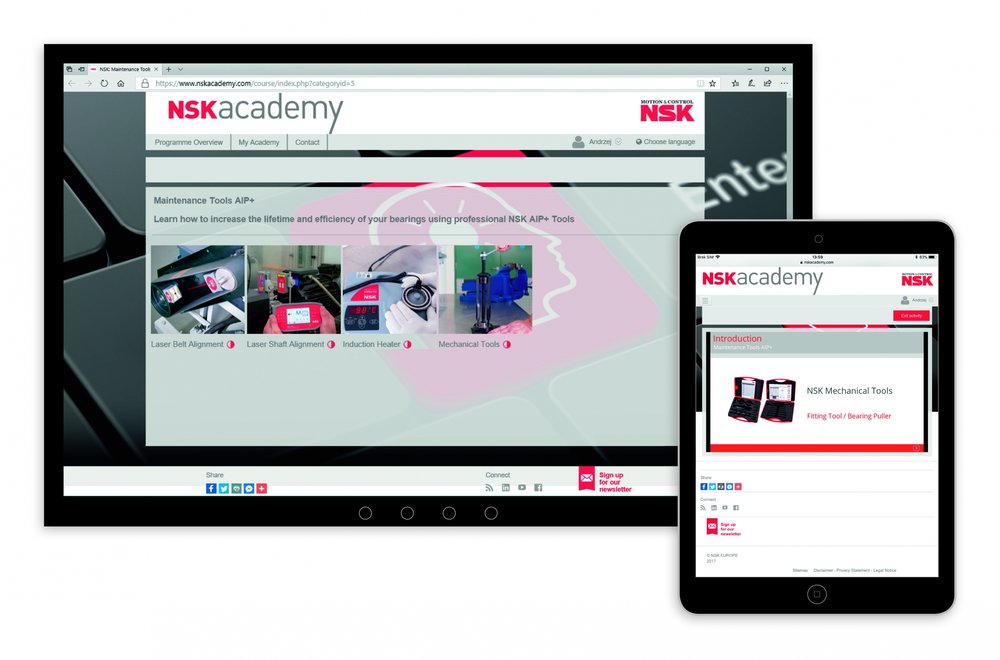
The Taptite 2000® generation of thread forming screws from Arnold Umformtechnik GmbH & Co. KB makes a fundamental contribution to cost reduction in threaded fastener systems (Figure 1). Based on experience, costs savings of up to 88% can be achieved in threaded fastener assembly.
According to the results of various studies, 85% of the total cost of a conventional threaded fastener joint arises from secondary costs such as drilling, thread cutting, inspection, tools and workstation cleaning. The actual fastening components account for only 15% of the total cost.
Here the thread forming screws of the Taptite 2000® generation offer decisive efficiency advantages, since costly assembly processes can be eliminated when these fastening components are used. In particular, non-cutting formation of the nut thread with Taptite® products makes them true ‘cost killers’. Furthermore, downstream operations such as cleaning and inspection are no longer necessary. Drilling operations can also be eliminated with pre-cast core holes, thus allowing total cost savings of up to 88% to be achieved in threaded fastener assembly.
Taptite 2000® users also benefit of the improved mechanical properties of the assembled joint. The trilobular shank form and radius-profile thread flanks result in around 50% lower thread forming torque than with conventional thread forming screws, which translates into higher clamping force together with a smaller statistical spread of clamping forces.
According to the results of various studies, 85% of the total cost of a conventional threaded fastener joint arises from secondary costs such as drilling, thread cutting, inspection, tools and workstation cleaning. The actual fastening components account for only 15% of the total cost.
Here the thread forming screws of the Taptite 2000® generation offer decisive efficiency advantages, since costly assembly processes can be eliminated when these fastening components are used. In particular, non-cutting formation of the nut thread with Taptite® products makes them true ‘cost killers’. Furthermore, downstream operations such as cleaning and inspection are no longer necessary. Drilling operations can also be eliminated with pre-cast core holes, thus allowing total cost savings of up to 88% to be achieved in threaded fastener assembly.
Taptite 2000® users also benefit of the improved mechanical properties of the assembled joint. The trilobular shank form and radius-profile thread flanks result in around 50% lower thread forming torque than with conventional thread forming screws, which translates into higher clamping force together with a smaller statistical spread of clamping forces.