www.mexicoindustrial.net
07
'22
Written on Modified on
MCLAREN RACING IMPRIME EN 3D 9000 PIEZAS AL AÑO CON LA TECNOLOGÍA DE ESTEREOLITOGRAFÍA DE ÚLTIMA GENERACIÓN DE STRATASYS
Con los tiempos y los presupuestos de producción de vehículos de F1 recortados por la FIA en 2022, McLaren recurre a un conjunto de impresoras 3D Stratasys Neo800 para ganar la «carrera» fuera de la pista.
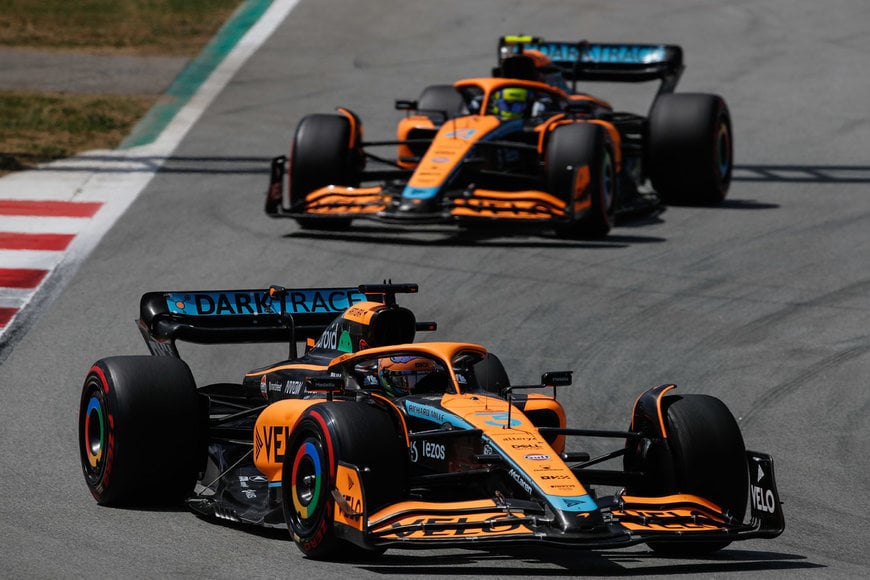
La impresión 3D reduce los tiempos de producción de algunas piezas de modelos a escala a solo tres días, lo que acelera rápidamente el desarrollo de vehículos.
La extrema precisión de las piezas en materiales poliméricos de alto rendimiento mejora las pruebas en el túnel de viento y permite a McLaren optimizar la aerodinámica y ahorrar segundos vitales.
Para responder al aumento de la exigencia de la FIA respecto a los límites de tiempo y presupuesto de producción de vehículos, McLaren Racing, el gigante de la Fórmula Uno, imprime en 3D decenas de miles de piezas con las grandes impresoras 3D de estereolitografía de nueva generación Neo®800 de Stratasys.
McLaren está ganando «la carrera antes de la carrera» al producir hasta 9000 piezas al año en numerosos programas de alerón delantero y trasero, así como grandes piezas de la carrocería lateral y la carrocería superior. La escudería consigue grandes avances en la optimización de la aerodinámica de los vehículos durante las pruebas en el túnel de viento, gracias a la precisión extrema de las piezas impresas en sus cinco sistemas Neo800. Además del aspecto cualitativo, el tiempo de producción de las piezas también se ha reducido drásticamente y ahora el equipo puede producir algunas piezas grandes, como modelos de carrocerías a escala, en tan solo tres días.
También es menos costoso. Debido a la incertidumbre y a la falta de ingresos en el mundo del deporte provocados por la Covid, la FIA decidió reducir el límite presupuestario de 175 millones de USD a 145 millones de USD para su primer año de actividad en 2021, después a 140 millones de USD para 2022 y 135 millones de USD en 2023.
El uso de la flota interna de impresoras permite a McLaren fabricar todas las piezas aerodinámicas en su base en Woking, Reino Unido, lo que ahorra costes de subcontratación y del proceso de control de calidad asociado. El equipo también puede imprimir en 3D guías y plantillas, así como moldes pequeños que anteriormente se mecanizaban a partir de placas de metal. La velocidad del proceso de estereolitografía de las Neo800 no solo ahorra un tiempo considerable, sino que también ahorra materiales metálicos costosos al no desperdiciar las grandes cantidades de virutas que se producen en el proceso de mecanizado sustractivo.
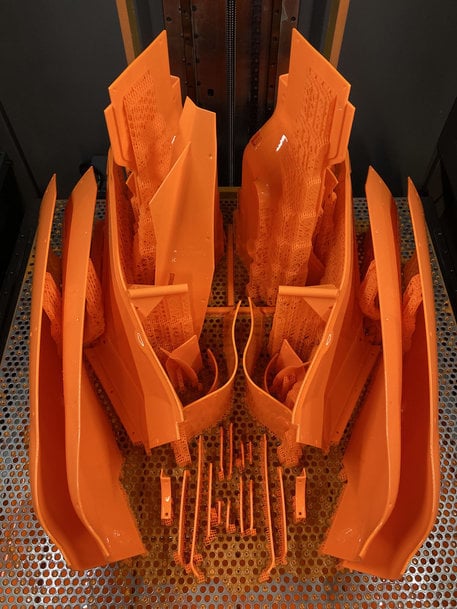
El uso de la tecnología de impresión 3D mediante estereolitografía de Stratasys puede ayudar a reducir los plazos de entrega de los proyectos y los componentes aerodinámicos en el túnel de viento, según McLaren.
Los avances en el túnel de viento marcan la diferencia
«La tecnología de estereolitografía y los materiales han evolucionado y han cambiado la forma en que los usamos», explica Tim Chapman, director de fabricación aditiva de McLaren Racing. «Ya no solo fabricamos prototipos; ahora producimos muchos componentes a gran escala y herramientas de tamaño completo».
Una de las aplicaciones principales en las que McLaren ve más valor con su Neo800 de última generación son las pruebas en túnel de viento. El equipo utiliza modelos a escala del 60 % para optimizar el paquete aerodinámico y encontrar más carga aerodinámica —que proporciona más agarre aerodinámico— y equilibrar las cargas aerodinámicas delanteras y traseras en el vehículo.
«Las pruebas en el túnel de viento siguen siendo el criterio de referencia cuando se evalúa cómo funciona cada superficie en conjunto, ya sea como un ensamblado o como un automóvil completo», explica Chapman. «Nuestra serie Neo de impresoras 3D nos ha ayudado a reducir drásticamente los plazos de entrega de nuestros proyectos y componentes aerodinámicos en el túnel de viento».
El equipo imprime piezas con el material de resina Somos® PerFORM Reflect, que se desarrolló específicamente para modelos de túnel de viento. Este material crea piezas fuertes y rígidas que necesitan un 30 % menos de tiempo para el postprocesamiento.
Chapman añade: «Descubrimos que los componentes de alta definición de nuestras máquinas Neo requieren un acabado manual mínimo, lo que reduce mucho el tiempo necesario para el procesamiento en el túnel de viento. Además de la velocidad, ahora podemos producir piezas para túnel de viento con una precisión, un detalle y un acabado superficial superiores, lo que ha permitido a nuestro equipo mejorar las pruebas y encontrar nuevas ideas innovadoras que mejoran el rendimiento. No podemos dejar de recalcar lo importante que son estos beneficios en la Fórmula Uno, con plazos muy ajustados de entrega de los vehículos para la próxima carrera y donde la más mínima iteración de diseño puede marcar la diferencia entre ganar, perder o recuperar posiciones en la parrilla».
El gran tamaño de la bandeja de las impresoras 3D Stratasys Neo800 (800 x 800 x 600 mm) permite crear piezas individuales grandes o una multitud de piezas mucho más pequeñas. Con este proceso, los detalles intrincados siempre se conservan con repetibilidad y fiabilidad líderes en el sector.
El mejor ejemplo es McLaren, que integra 50 o 60 carcasas de presión de aire en sus vehículos de carreras para permitir lecturas de presión de aire en diversas superficies. Las pequeñas tomas de presión que atraviesan estos componentes son muy intrincadas y detalladas, y se asientan dentro del vehículo durante las pruebas y carreras para permitir que los ingenieros controlen y optimicen continuamente el rendimiento aerodinámico.
Andy Langfeld, presidente para EMEA de Stratasys, lo explica: «El valor transformador de la impresión 3D proviene de poder personalizar y adaptar piezas rápidamente para aplicaciones específicas. En este caso, McLaren ha podido acortar drásticamente el tiempo de desarrollo del producto y controlar los costes con la tecnología de estereolitografía de última generación de Stratasys, que se combina con los materiales Somos de primera categoría y nuestra amplia experiencia en el mundo de las carreras. Es una gran colaboración entre dos organizaciones de nivel mundial».
www.stratasys.com