www.mexicoindustrial.net
06
'21
Written on Modified on
The Robot Revolution in Manufacturing Industry
In a short span of 60 years, robots have revolutionised manufacturing and emerged as game changers in industry.
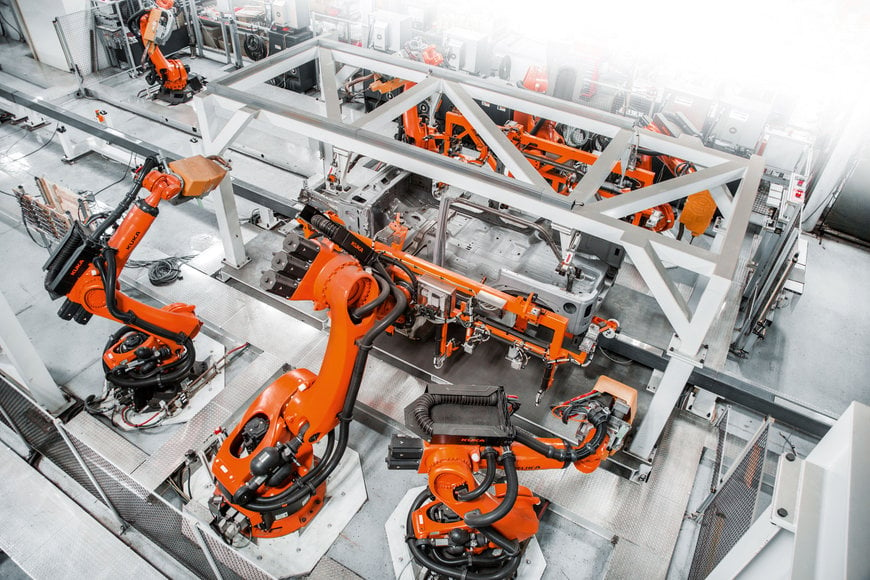
The term ‘robot’, with Slavic roots denoting labour, was first used in 1920 by Czech writer Karel Čapek in a play about a factory making artificial humans for work. But even before the term was coined, the concept has fascinated human beings from ancient times, with various civilisations exploring the idea of mechanised human forms as servants and companions. Leonardo da Vinci’s Mechanical Knight from the Renaissance period was perhaps the best representation of this effort. The quest gained momentum with the advent of the First Industrial Revolution in the latter half of the 18th Century, when mechanisation actually began replacing human labour. The honour for designing the first modern programmable robot however goes to George Devol, an American inventor who designed a programmable mechanical arm, later called the Unimate. Devol worked to refine this further with Joseph Engelberger, his contemporary and fellow inventor, who is today acknowledged as the ‘Father of Robotics’. The Unimate was an autonomous, pre-programmed robot designed to perform a task repeatedly. It was first installed in 1961 by General Motors at its factory to move pieces of hot metal. There was no looking back, as the cliché goes, and the evolution of the modern industrial robot truly began.
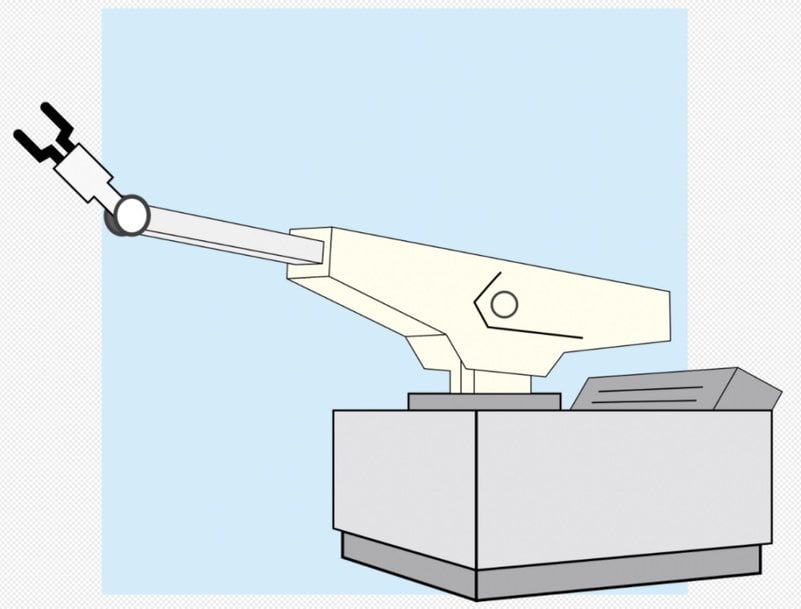
In a short span of 60 years, robots have revolutionised manufacturing and emerged as game changers in industry. Today technologically advanced companies and countries are maintaining their edge over the less robotically inclined, with dramatic results.
According to the World Robotics 2020 Industrial Robots report released by the International Federation of Robotics (IFR), a record of 2.7 million industrial robots are operating in factories around the world. The average robot density in the manufacturing industry today has hit a new global record of 113 units per 10,000 employees. The world’s top 10 most automated countries (in descending order) are: Singapore, South Korea, Japan, Germany, Sweden, Denmark, Hong Kong, Taiwan, USA and Belgium and Luxemburg. The fact that all these countries are known for their technological prowess is no coincidence. Singapore has the highest robot density in the world with 918 units per 10,000 employees. China, with robot density of 187, is the fastest growing market, while Japan (robot density 364) is the largest manufacturer of industrial robots accounting for 47% of global production.
The growing popularity of robots
There is no single factor behind the increasing adoption of robots in manufacturing. The most common advantages of robots over their human counterparts are by now too well known – speed, precision and accuracy, besides the ability to operate in hazardous locations. Robots do not get tired, do not make mistakes and do not report sick or need vacations. Together, these attributes have worked well in increasing production efficiency manifold, while at the same time reducing costs significantly.
“There are a lot of things all converging at the same time to create a ‘perfect wind’ for the growing acceptance of robotics. It starts with the internet age and netizens wanting more product choice and shorter delivery periods. This drives the need for faster response from manufacturers but also the need to ensure there are no lapses in quality, and robots are a natural choice to solve both points,” says Chris Hazlewood, Chief Editor, Factory Automation Promotion Group at Mitsubishi Electric. “In parallel, there has been a major expansion of potential robot applications. No longer are robots restricted to an isolated cell to perform high speed processes, robots and humans are now working side by side. This has been made possible because many of the understandable human safety issues are resolved through new collaborative robot concepts, the use of AI vision systems to make adaptive path decisions and protective solutions like ‘soft skins’ around the robots – all of these innovations reduce the fear factors, increase the usability and speed up the adoption. And finally, there is the realisation in many countries that there are concerns about the future available workforce as the population ages and skills are potentially lost, so again robots are a natural solution to this,” Chris elaborates. Mitsubishi Electric’s line of industrial robots offers high performance and reliability to address demanding applications across many industries.
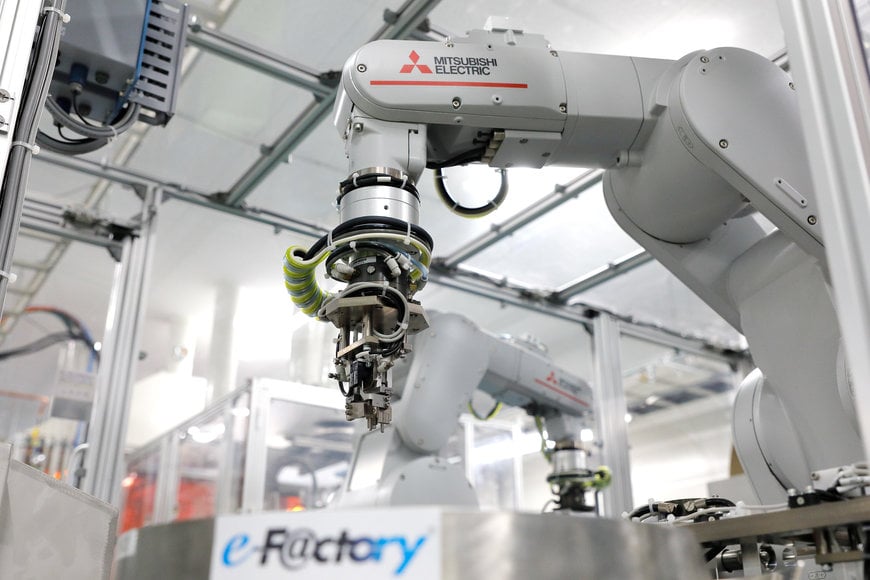
“Robots offer numerous advantages. They are predestined for repetitive tasks because they work with the highest precision and around the clock without getting tired. They give people the time to tackle more demanding tasks. They compensate for the lack of skilled workers. In times of crisis, these advantages come into their own, also because a lot of thought is given to new applications,” says Michael Otto, Chief Sales Officer of KUKA Robotics, the world's leading provider of production systems in the automotive industry. The company, part of the Midea Group, is the third largest manufacturer of robots in the world. Its KR QUANTEC series perhaps has the widest load range spanning from 90kg up to 300kg with a reach of up to 3100mm, with applications across industry segments. However, in other ranges, the company has industrial robots with up to 1000kg capacity. This is also true of other major OEMs in the segment.
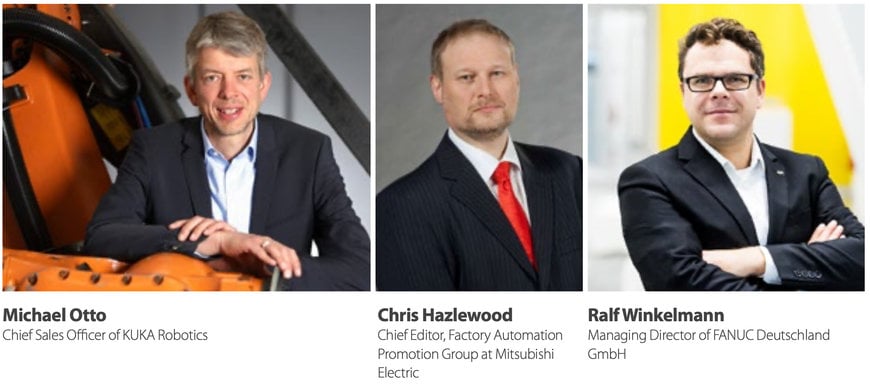
The largest user industry
The automotive industry, which was the first to adopt assembly line production in 1913 with the Ford Model T, is also the largest user of automation and robotics today. Close to a third of all industrial robots are used in the automotive industry. A recent IFR report highlights this fact clearly. For example, Germany has a robot density of 346 for general industries, but its automotive industry has a robot density of 1,311. Similar proportion is reflected in the statistics for the US and Japan, the two other leading automobile manufacturers, and China is catching up fast. Other than assembly operations, robots in automobile industry are deployed for critical tasks like welding/gluing, painting, machine tending, material handling, pick and place, etc. The auto components industry is also a major user of robots in machine tending and parts transfer operations.
At the China International Industry Fair in late 2020, ABB showcased several intelligent products and technologies for the automotive industry, including automotive electronics assembly, quality inspection and an innovative new PixelPaint solution. This uses an inkjet to eliminate overspray, enabling two-tone paint and individual designs to be applied in one pass, without masking and de-masking, making customised painting 50 per cent faster and more sustainable. For the record, ABB is the world’s largest manufacturer of industrial robots with a very wide range of models and applications, and the largest installed base of any robotics manufacturer.
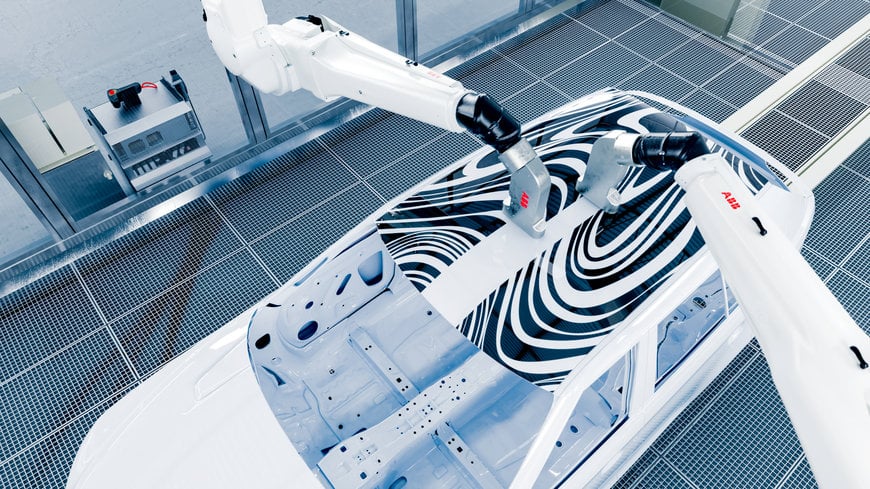
Other industry segments that use robots extensively include electricals and electronics; white goods and appliances, metal and machinery; plastic and chemicals; and food & beverages. As for applications, packaging and palletisation is one of the major areas for use of industrial robots, as are material handling and warehousing. Robots today are not just automated mechanical devices but also rapidly gaining capabilities with increasing use of many types of sensors, especially machine vision. This, coupled with artificial intelligence and machine learning, are adding more critical applications in various other industries and processes, like the healthcare sector.
Adapting to change
With the impending electrification of automobiles, one major concern is how will the rising popularity of Electric Vehicles impact use of robots in automotive industry, which is one of the largest users? This is especially relevant because EVs have fewer parts and assemblies, and hence are expected to cause a significant change in the process of automobile manufacturing. All major automotive companies today offer the EV option, or are in the process of launching one. That the future of mobility is electric, is now evident going by the emerging trends. But robots will remain on the shop floor even as the industry goes green with EVs, since the automobile industry is now more than ever reliant on advanced manufacturing technologies.
This is best illustrated by how automation specialist and industrial robot manufacturer FANUC supports Volkswagen in the expansion of future-oriented drive technologies. In September 2020, the company announced it is supplying a total of around 1,400 robots to the VW plants in Emden, Germany, and Chattanooga, USA. The FANUC robots will be used in body shop and battery production. “The demands on robot technology have changed due to the construction of electric vehicles,” says Ralf Winkelmann, Managing Director of FANUC Deutschland GmbH. “Thanks to our wide range of products, we can react to them reliably and flexibly.” The VW site in Emden is currently being transformed into one of the most modern locations in the automotive industry. From 2022, more than 800 FANUC robots will produce a new generation of VW e-vehicles there. The plant in Chattanooga will be expanded to become the centre of VW's production of e-vehicles in North America. Starting in 2022, Chattanooga will employ approximately 600 additional FANUC robots. As the world’s fourth largest manufacturer, FANUC, also a strategic partner of BMW, offers more than 100 robot models, the widest range of industrial robots with payload ranging from 0.5kg-2300k, for any application or industry.
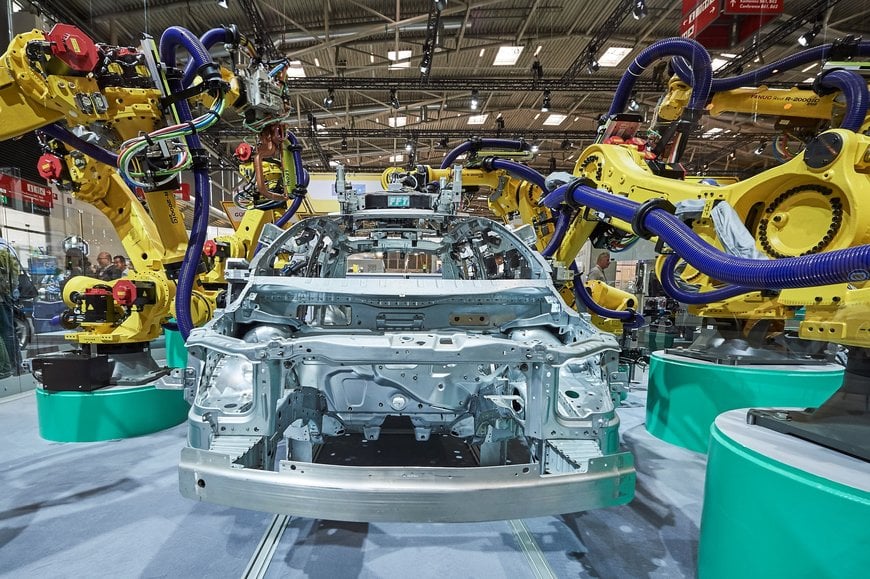
Italian industrial automation company Comau, with its wide range of industrial robots, has provided FCA and the Fiat brand with advanced automation solutions for the development of its first fully electric vehicle, the New 500. A total of 187 Comau robots are integrated in the different phases of the car manufacturing process, thanks to the collaboration of a team of Comau experts who worked side-by-side the automaker’s designers to optimise the work lines for Smart Manufacturing. Each robot has been fully equipped by Comau to efficiently carry out all the special processes an electric car requires – from custom-designed handling systems and grippers to a special 3D printed end-effector for moving body components.
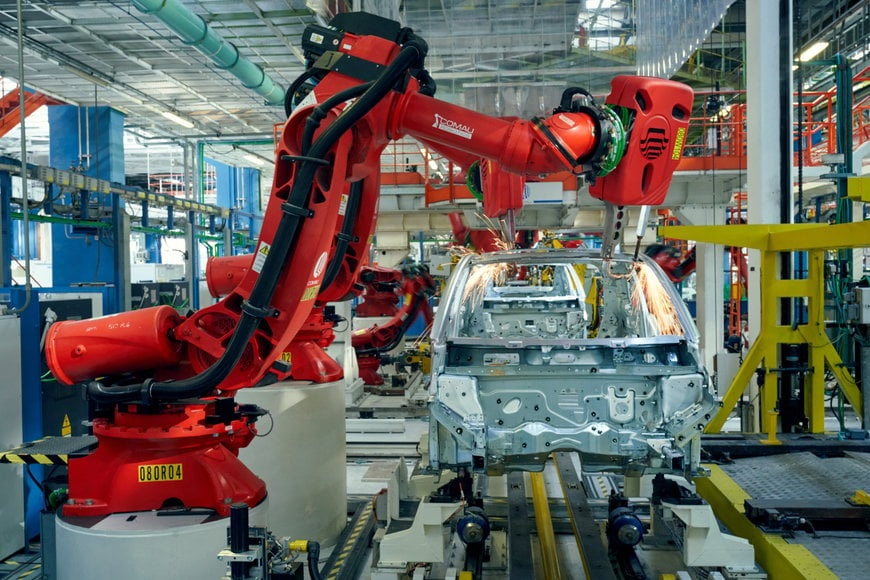
Comau has also integrated the lines with advanced vision systems to control the quality of the adhesive dispensing system, both during processing and at the end of the cycle. In order to optimise and speed-up inline tool changes, an articulated magazine system was designed to provide the robots with the different types of tools required to perform each application in a fast and easy way. Says Andrew Lloyd, Chief Operating Officer – Electrification of Comau: “Our experience and global leadership in the industrial sector, together with the skills gained in the field of electrification and digitalisation, support the creation of highly innovative, flexible and tailor-made technological solutions. This approach allows Comau to develop projects that look to the future of mobility and renewable energy sources, such as the New 500 full electric, thus responding to the needs of an industrial system in continuous evolution and the demands of an end consumer increasingly attentive to sustainability.”
“When you think of the automotive industry and robotic use you probably imagine big robots lifting and welding panels or applying the painting processes that give the car its impressive finish. Actually, robots are used on multiple other areas from haptic testing of the drivers’ console, through to assembly of multiple subcomponents and electronics. In our showroom in Akihabara, Tokyo we even demonstrate the assembly of the in-car entertainment system, by robots,” says Chris Hazlewood. “Furthermore, I saw recently a very innovative use of robots to change car tyres in a shorter time and with recordable security that each wheel, nut and tyre have been correctly installed. The reason I relate these examples is each of these applications will still remain regardless if it will be a fossil fuel engine or an EV. In addition, I also think these examples illustrate just how innovative automotive manufacturers are at utilising automation to gain production flexibility and advantage. It’s a trend I don’t see changing and if anything, accelerating as robots may gain new tasks in the building of electrical motors, installation of battery systems, etc.,” adds Chris.
What are the future trends for robots?
In the next ten years, more and more people around the world will be working with robots. Automation is becoming mainstream and is finding its way into more and more areas. “Our mission by 2030 is: Automation will be simpler, more intuitive, and thus available to everyone. This will lower the entry threshold. Programming a robot will then be as easy as working on a PC today,” says Peter Mohnen, CEO KUKA Group. According to Mohnen, the increasing width of applications is evident in other industries: “After the coronavirus pandemic, there will be a real push towards more automation, especially in logistics and healthcare, which will have a major impact in the medium term.” Easy access to robotics is KUKA’s ambitious goal – and the company will present the first elements of a preview of an operating system of the future at the Hannover Messe 2021 Digital Edition. Because therein lies the key: simple operation and intuitive handling of automation solutions, which until now have often been reserved for experts.
“Smart robotics and automation are vital to deal with new consumer trends, demand for product variety or challenges from trade barriers,” says Dr Susanne Bieller, General Secretary of the IFR. “New technological solutions pave the way for more flexibility in production.” Simplification, Collaboration and Digitalisation are key drivers that will benefit robot implementation. Programming and installation of robots has become much easier with digital sensors combined with smart software that allow direct teaching methods, the so-called ‘Programming by Demonstration’. The task that the robot arm is to perform is first executed by a human. The human operator literally takes the robot arm and hand-guides it through the movements. This data is then transformed by the software into the digital program of the robot arm. According to the IFR, in future, machine learning tools will further enable robots to learn by trial-and-error or by video demonstration and self-optimise their movements.
In fact programming of robots is becoming easier across the OEMs. ABB has launched its Wizard Easy Programming software for its IRB 1100 industrial robot, allowing first time users to introduce robotic automation into their production lines without the need for specialist programming skills or any knowledge of RAPID code. “There is a growing demand from industry for robots that can be programmed easily for a wide range of tasks, which is why ABB is expanding the capability of Wizard Easy Programming to support small industrial robots starting with the IRB 1100,” said Antti Matinlauri, Head of Product Management for ABB Robotics. “People have become accustomed to the easy user interfaces in smartphones and other consumer technology. Our Wizard Easy Programming tool uses this concept to take the effort out of programming industrial robots and brings us a step closer to enabling anyone and everyone to use robotics.”
“Robots will become smarter, more connected, more mobile and more ‘normal’. They will become an ever increasingly familiar sight not only in manufacturing but in our everyday life, from shelf management in the supermarket, to hotel concierge functions and even serving your coffee. Many of these activities are being pioneered now but will mature and become more widespread in the world of tomorrow,” says Chris Hazlewood. Referring to the role of artificial intelligence and machine learning, he adds, “AI and ML will not be something unusual or to be feared, but a background function that enables and supports. Customers will not be looking to buy an AI enabled device but to buy a smart device to fulfil specific tasks.”
Conclusion
The global economic crisis in the wake of Covid-19 pandemic is expected to shape industrial robot sales in 2021. The 2020 sales of industrial robots were impacted marginally due to the crisis, which is a temporary phenomenon. Digitalisation has unleashed the next wave of automation with emerging technologies helping robots to become even more agile and versatile. The Covid-19 pandemic has also brought home the need for more autonomous factory operations in future, and hence the long term prospects for industrial robots remain excellent.
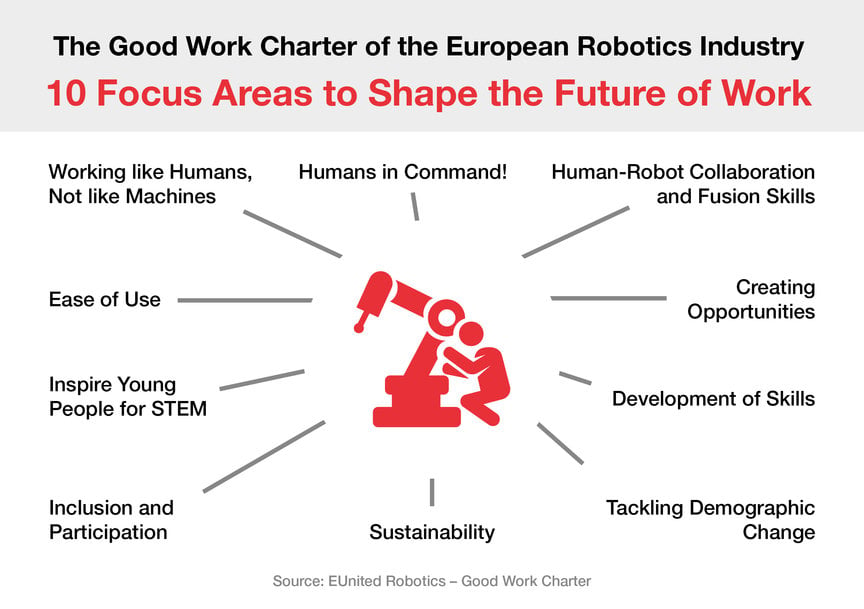
European Charter for Robots and Humans
The European charter for robots and humans working together has been officially released by the European Engineering Industries Association (EUnited) earlier this year. The document defines 10 focus areas to shape the future of work. The charter supports the UNITED NATIONS Sustainable Development Goals (SDGs) for 2030.
“The transition to an increasingly automated and data driven economy requires changes in work arrangements that need to be adjusted by employers, their workers and government,” says Nobel Prize laureate, Sir Christopher Pissarides, Co-Chair at the Institute for the Future of Work (IFOW). “Industry can help by ensuring that their workers are equipped with the skills and knowledge to thrive in the new economy.”
Focus area one puts the human in the centre: The charter wants robots to relieve workers of the dull and low-interaction work that is not well suited for human nature - employees should work like humans and not like machines. Focus area two makes it clear that robots must assist humans, not the other way around. Therefore, the European robotics industry advocates a “human-in-command approach”. The other focus areas deal with skills development, human-robot collaboration, the ease of machine use, initiatives especially for young people and strategies tackling demographic change.
“2.7 million industrial robots in use worldwide and the increasing use of service robots outside factories rapidly change the way we work,” says EUnited Robotics Chairman, Wilfried Eberhardt. “To actively manage this transition, the European robotics industry has developed the ’Good Work Charter’ and identified 10 focus areas that we need to address now. It is essential to understand that humans will always play a central role in the workplace.”
Released by Engineering Association EUnited, the European Charter for robots and humans uts the human in the centre.