www.mexicoindustrial.net
02
'13
Written on Modified on
Las nuevas y mejoradas fresas radiales de cerámica dura EADE™ de Kennametal son el nuevo referente de velocidad y vida útil para el mecanizado de aleaciones de alta temperatura a base de níquel
Por primera vez la industria muestra reducciones espectaculares en el mecanizado de paletas de turbina y otros componentes de las industrias energética y aeroespacial
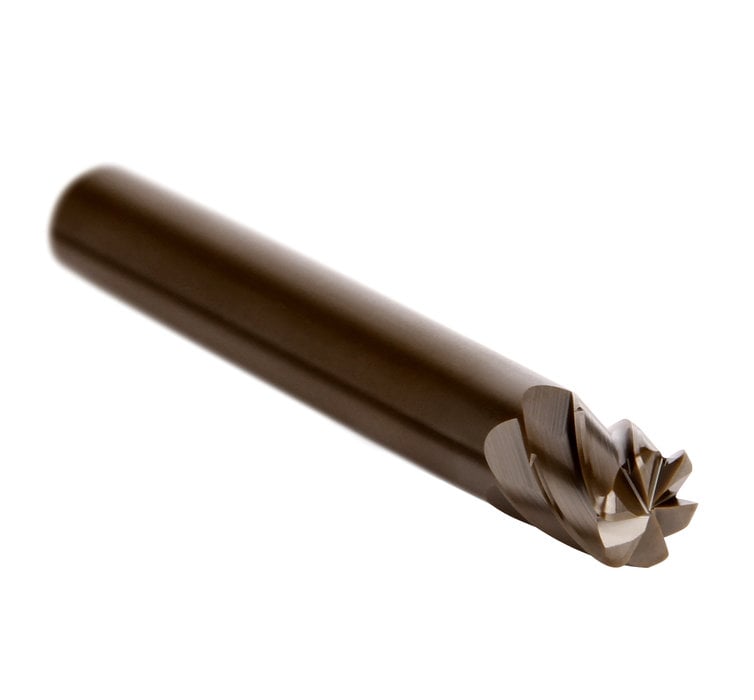
La nueva y mejorada fresa radial de cerámica dura y 6 dientes KYS40 de Kennametal.
Quizá el supuesto más básico en el mecanizado sea que para cortar materiales de alta resistencia se requieren herramientas más resistentes. Las aleaciones a base de níquel patentadas que se utilizan en turbinas de gas y vapor son, por ejemplo, unos de los materiales más resistentes del mundo y están en constante desarrollo para permitir que centrales eléctricas funcionen a temperaturas mucho más altas. Esto no solo ofrece más energía a quienes lo necesitan, sino que aumenta el rendimiento de la central y reduce o elimina las emisiones nocivas. Las superaleaciones como Inconel®, Waspaloy® y Rene®, entre otras, entran en juego cuando se trata de paletas de turbina y otras piezas que requieren alta resistencia, excelente resistencia a la fluencia a altas temperaturas, estabilidad de fase y resistencia a la oxidación y a la corrosión.
Pero mecanizar dichos materiales puede resultar lento, laborioso y caro. En general, las herramientas de metal duro integral funcionan normalmente a una velocidad de entre 65 y 200 SFM (20 a 60 m/min) en materiales con una vida útil limitada. No obstante, las nuevas fresas radiales de cerámica dura y calidad KYS40TM de Kennametal presentan mejoras en órdenes de magnitud en el mecanizado de aleaciones a base de níquel de alta resistencia, desbastando a una velocidad de corte de hasta 3.300 SFM (1000 m/min) y siendo su vida útil entres dos y tres veces mayor que en caso de las herramientas de metal duro integral comparables.
Las primeras de la industria
Las herramientas de corte fabricadas en cerámica, principalmente en óxido de aluminio (Al2 O3), llevan existiendo desde principios del siglo XX. En 1913 se expidieron en Alemania las patentes para las herramientas de corte de cerámica que fueron comercializadas en EE. UU. en los años 50. Hoy en día siguen utilizándose plaquitas indexables de cerámica porque pueden operar a una velocidad más alta en determinadas aplicaciones, pero las fresas radiales de cerámica dura se ven en raras ocasiones, ya que al ser más frágiles que el metal duro su rendimiento no es bueno. De hecho, muchos fabricantes de turbinas han optado por producir sus propias fresas radiales de metal duro integral por lo mucho que consume este tipo de herramienta.
La nueva calidad de cerámica SiAlON KYS40 de Kennametal y el diseño global de la fresa radial de cerámica dura suponen ahora la forma más eficaz para el desbaste de aleaciones de alta temperatura a base de níquel. “En superaleaciones a base de níquel, la velocidad de corte puede ser hasta 20 veces superior en comparación con las fresas radiales de metal duro integral y, además, debido a la excelente resistencia térmica de la cerámica y a los filos de corte más resistentes (ángulo negativo), la vida útil de la herramienta puede llegar a multiplicarse por cinco e incluso más”, indica Thilo Mueller, responsable de producto global en Kennametal.
Hay disponibles dos tipos de fresas radiales de cerámica dura KYS40: la de seis canales para el refrentado y el perfilado, y la de cuatro canales con cuello para trabajos de ranurado y en cavidades. Ambas líneas de producto son aptas también para rampas, interpolaciones helicoidales y estrategias de mecanizado trocoidal.
Los mecanismos de desgaste y la indicación de desgaste en las fresas radiales de cerámica dura, completamente diferentes a los de las fresas de metal duro, permiten trabajar con fresas radiales de cerámica en aplicaciones en las que sería necesario sustituir las herramientas de metal duro. Esta es una de las razones por las que la nueva fresa radial de calidad KYS40 es desechable y su uso va más allá del desgaste ordinario.
Mecanizado de paletas de turbina
Bien impulsadas por combustibles fósiles, agua o energía nuclear, casi todas las centrales eléctricas del planeta utilizan turbinas para generar energía. Producir, gestionar y mantener estos componentes fundamentales es vital para mantener el flujo energético.
Esto ejerce mucha presión sobre los fabricantes que deben actualizar constantemente sus estrategias de mecanizado. Son muchos los factores que influyen: ¿Qué hace falta? ¿Muchas paletas similares, o pocas paletas pero de diseño diferente? ¿Hacen falta centros de mecanizado y configuraciones múltiples, o máquinas multitarea y multieje? ¿Qué sistema CAD/CAM está siendo utilizado y cuál es la experiencia de los operarios?
Y, por supuesto, ¿cuáles son las mejores opciones de utillaje para las operaciones de mecanizado? Los resultados de las pruebas llevadas a cabo recientemente con la nueva fresa radial de cerámica dura KYS40 son perspicaces.
En primer lugar, la cerámica de calidad mejorada KYS40 en versión de cuatro y seis canales incorpora un núcleo más grande que mejora la rigidez de herramienta y reduce la flexión en velocidades de corte más altas. Los extremos con geometría optimizada y el ángulo helicoidal de 40 grados aumentan la acción de corte y la evacuación de virutas.
Al desbastar el perfil de una paleta de turbina fabricada en Inconel 718 mediante mecanizado en seco, la fresa radial de cuatro canales EADE funcionaba a 645 m/min (2116 SFM) con una avance de 0,03 mm/z (0,0012 IPT). La profundidad de corte (ap) era de 0,5 mm (0,0197 pulgadas) y la anchura de corte (ae) de 11,4 mm (0,866 pulgadas). En comparación con las soluciones convencionales, la fresa de cuatro canales duró tres veces más desbastando en menos tiempo. Esta aplicación triplicó las piezas producidas por fresa.
La fresa radial de cerámica dura EADE fue probada perfilando un blisk (disco con paletas integradas), fabricado en Inconel 718, y utilizando aire comprimido para la evacuación de las virutas. A diferencia de las herramientas convencionales de metal duro, en el desbaste para dar al componente su geometría final, se crean virutas más parecidas al polvo que las virutas rizadas tradicionales, por lo que solo se requiere aire comprimido para retirarlas de la zona de corte. Las condiciones de prueba eran las siguientes: velocidad de corte de 679 m/min (2228 SFM), avance de 0,03 mm/z (0,0012 IPT) y profundidad de corte variada de hasta 0,5 mm (0,0197 pulgadas).
Se consiguieron dos segmentos de blisk mecanizados, utilizando una sola herramienta siendo necesarios 12 minutos por segmento, hecho que el personal calificó como 'sin precedentes'”.
Las nuevas fresas radiales de cerámica dura EADE también están incluidas en la nueva aplicación “Kennametal Innovations” para iPad que puede descargarse gratuitamente en la App Store de iTunes™. Es muy sencillo navegar por la aplicación y realizar búsquedas introduciendo palabras clave para encontrar soluciones específicas para herramientas y determinados grupos de producto. Principales características:
-Animaciones de producto que ofrecen una representación visual clara de los procesos, con vínculos directos para obtener información detallada.
-Un mapa de navegación con menús desplegables donde se ofrece información adicional, incluyendo tablas y gráficos que pueden personalizarse y ampliarse.
-Navegación orientada a los usuarios que, gracias a la posibilidad de seleccionar los datos, permite realizar rápidamente las comparaciones necesarias para obtener productos competitivos y de calidad.
-Demostraciones y vídeos para conseguir una experiencia real y valiosa y conocer las tecnologías que actualmente se están utilizando para las herramientas.
Kennametal ofrece sus nuevas fresas radiales de cerámica KYS40 en rangos de entre 3/16 y ½ pulgadas (4-12 mm). Para trabajar con la herramienta no se requiere ninguna fijación especial, es suficiente con un mandril, plato mecánico o hidráulico de alto rendimiento, aunque el plato debe ser capaz de funcionar a las altas velocidades necesarias para el mecanizado de superaleaciones. Para garantizar la máxima vida útil de herramienta, se recomienda un equilibrado de precisión. Más información en www.kennametal.com.
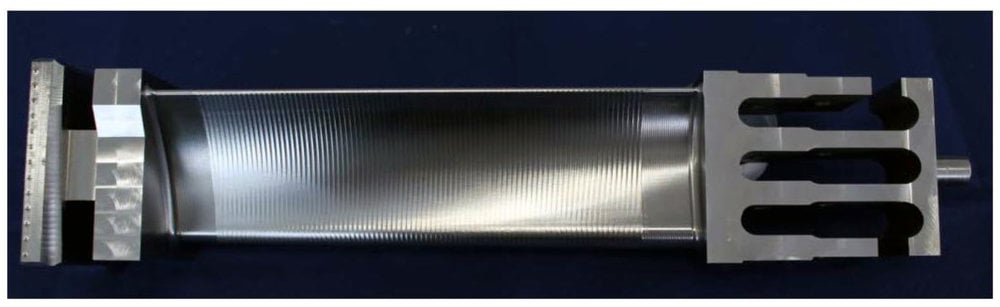
Las paletas de turbina fabricadas en superaleaciones a base de níquel suponen un reto al tratarse de complejas tareas de mecanizado. Las nuevas fresas radiales de cerámica dura de Kennametal son el nuevo referente en cuanto a la velocidad de mecanizado (véase a continuación) y vida útil de herramienta.
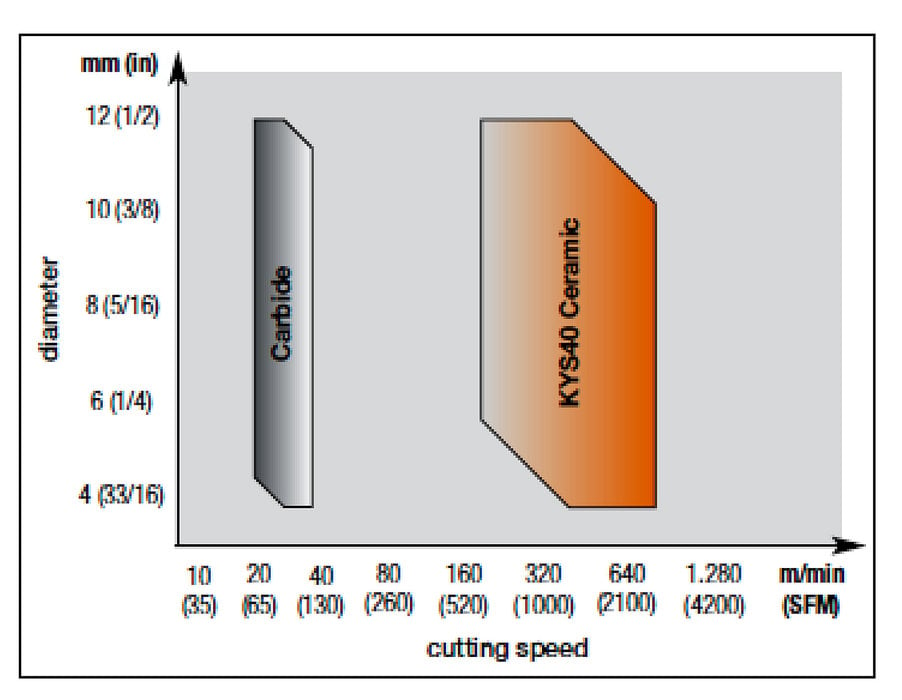