www.mexicoindustrial.net
23
'12
Written on Modified on
La evolución de ARPRO® ayuda a los diseñadores de automóviles a perder peso
La reducción del consumo energético global pasa por minimizar el gasto de combustible en los vehículos, el cual está muy ligado a su vez al propio peso del vehículo. La nueva tecnología inrekor, que integra un núcleo de ARPRO®, consigue no solo que el vehículo sea más ligero, sino también una excepcional resistencia en caso de impacto así como excelentes niveles de elasticidad y compatibilidad con múltiples materiales. Su implantación en todo el parque automovilístico mundial permitiría ahorrar miles de millones de litros de combustible al año.
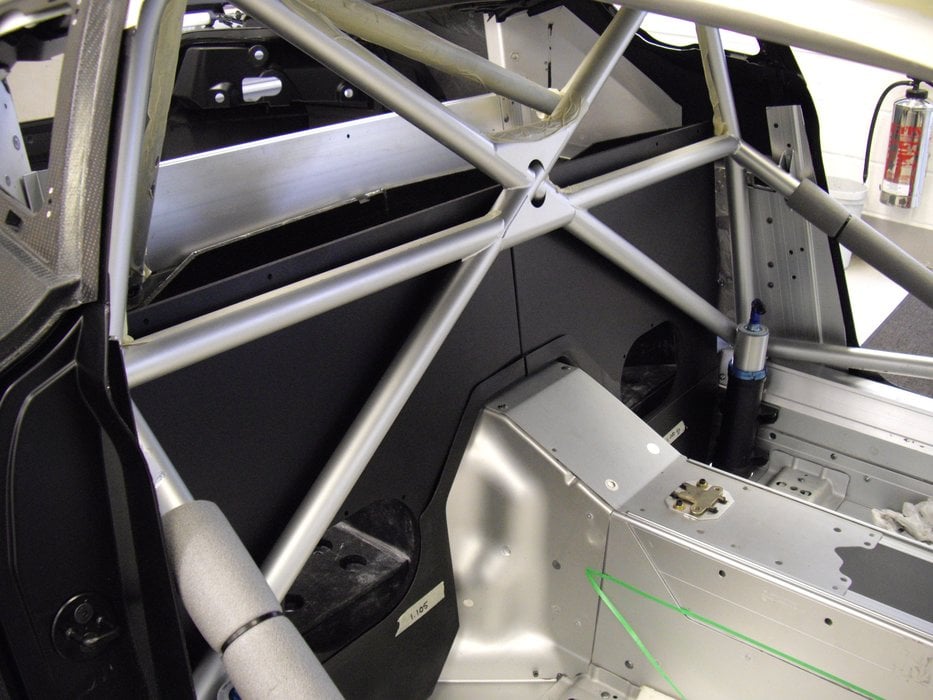
Gerente de Desarrollo y Ventas de Aplicaciones para Europa, África y Oriente Medio de JSP
El sector de la automoción lleva desde la década de 1980 buscando métodos que permitan reducir el peso de los vehículos y el consumo de combustible sin poner en riesgo el rendimiento ni la seguridad, una búsqueda que ha permitido desarrollar un gran número de nuevos materiales ligeros para aplicaciones estructurales en los vehículos.
Posiblemente, la innovación más importante en este campo ha sido el desarrollo del polipropileno expandido (EPP). Este material, que se fabricó por primera vez a finales de la década de 1980, forma parte del parque automovilístico europeo desde hace más de veinte años. A diferencia de otros materiales desarrollados con anterioridad, cuyas características de absorción de energía eran cuestionables, el EPP gozaba de dos características físicas fundamentales que rápidamente lo convirtieron en un material de referencia en el ámbito de la protección frente a impactos a baja velocidad.
En primer lugar, su estructura de espuma de célula cerrada lo convierte en un material isotrópico, es decir, que presenta las mismas propiedades independientemente de la dirección en la que reciba el impacto. Este hecho contrasta radicalmente con los productos fabricados con poliuretano rígido o moldeado por inyección, cuyo rendimiento se limitaba tradicionalmente a un único escenario de colisión. Su otra ventaja consiste en su capacidad para recuperar su forma original tras deformarse una y otra vez; de ahí que sea ideal para las aplicaciones de protección frente a impactos a baja velocidad. Todas estas características permitían al material satisfacer sobradamente los exigentes requisitos de rendimiento impuestos tanto por los gobiernos como por el sector, como por ejemplo los requisitos de seguridad pasiva de las pruebas del EuroNCAP.
Durante la década de 1990 se desarrollaron por primera vez calidades especializadas, como por ejemplo productos porosos y dotados de resistividad de superficie discreta, y el material se fabricó en varios colores.
Los diseñadores de vehículos se apresuraron a aprovechar las oportunidades que toda esta gama de productos ofrecía, por lo que hoy día es frecuente encontrarlos en diversos componentes de los vehículos. Entre sus aplicaciones cabe citar los productos de seguridad pasiva como puertas, absorbedores de energía laterales, paneles de puertas, reposacabezas, núcleos de asientos, protección de los asientos y frente a impactos en las rodillas, así como en aplicaciones de almacenamiento. A este respecto, su excepcional relación resistencia/peso permite su uso en sistemas de almacenaje de juegos de herramientas, revestimientos de maletero, suelos de carga o componentes de las consolas. Por ejemplo, resulta sencillo crear un revestimiento de maletero con volumen suficiente como para ocupar el espacio requerido (y que por lo tanto no se mueva durante el transporte) pero sin que suponga un aumento significativo del peso. Además forma parte de la sustancia estructural del maletero, por ejemplo ayudando a absorber la energía de los impactos durante una colisión en la parte trasera. La misma aplicación con productos moldeados por inyección no solo exigiría costosos procesos de mecanizado, sino que además supondría un aumento significativo del peso y una contribución mucho menor a la estructura. La actual gama de polipropileno expandido es apta para cualquier aplicación en donde la estética no sea la principal prioridad y no exista riesgo de exposición continuada a la luz ultravioleta.
Las piezas moldeadas en polipropileno expandido también se utilizan ampliamente en las aplicaciones de relleno para el transporte de componentes frágiles entre fábricas y plantas de montaje, lo que minimiza el porcentaje de residuos debido a los daños en tránsito y permite recuperar la inversión con rapidez. No es raro que los livianos contenedores para relleno de un determinado vehículo sobrevivan al ciclo de fabricación de dicho vehículo. Las alternativas son los palets de madera, más baratos pero también más difíciles de moldear, o el acero, que ofrece una buena protección física pero puede dañar los componentes debido a una excesiva transmisión de fuerzas causadas por las vibraciones o los golpes.
Importante reducción de peso
En algunas aplicaciones, como los asientos, se consigue una reducción total del peso de hasta un 35% en relación con los sistemas alternativos, además de una mayor flexibilidad de diseño, lo cual permite consolidar piezas y servir de complemento de otros materiales en caso necesario. Los costes del mecanizado son notablemente inferiores a los del moldeo por inyección, mientras que los productos de bajo peso ofrecen la posibilidad de desmoldear elementos negativos sin necesidad de realizar inversiones adicionales en mecanizado. Por otro lado, la capacidad para crear piezas que se ajustan a la perfección entre sí proporciona una mayor libertad de diseño y compatibilidad con otros materiales. Un buen ejemplo de es la serie 5 de BMW , donde el uso de ARPRO permitió adoptar una solución para el asiento trasero que redujo la inversión en mecanizado, los plazos de entrega y el peso de los componentes.
La mayor moldeabilidad, que permite una mayor libertad de diseño, ha sido de hecho uno de los avances más importantes en este tipo de materiales desde su adopción hace más de veinte años. Los nuevos avances en materiales y la mejora en las soluciones de mecanizado han ampliado las posibilidades de moldeado en 3D y han permitido crear productos más pequeños y finos. Los clientes pueden optar por una amplia gama de calidades por densidad, lo que les permite lograr la formulación más adecuada con el consumo de vapor y los tiempos de ciclo más bajos posibles. Por ejemplo, las viseras de protección solar, que tienen que superar una prueba de impacto en la cabeza ya que se les considera un elemento de seguridad fundamental, pueden moldearse con facilidad ya que las innovaciones en cuestión de materiales de base han permitido obtener tamaños de perla más pequeños con los que es posible fabricar secciones más finas, lo que a su vez redunda en una presencia mínima de huecos en la superficie acabada.
Los avances más recientes han permitido obtener asimismo productos que proporcionan unos menores niveles de residuos así como menos tiempo “perdido” durante la puesta en marcha de las herramientas y el ajuste fino del proceso al inicio de las tiradas de producción. Por lo que respecta a la estética, también se están produciendo avances a buen ritmo. Los productos más recientes presentan toda una gama de acabados de superficie de textura cálida y uniforme, lejos del aspecto rugoso de la materia prima, cosa que jugará un papel fundamental en la reducción del número y el peso de los componentes, por ejemplo en las áreas visibles “secundarias” donde la exposición limitada a la luz ultravioleta evita la necesidad de aplicar revestimientos.
Vida útil más larga de la batería en vehículos eléctricos gracias a inrekor
La irrupción de los vehículos eléctricos representa una clara oportunidad, dada la necesidad de reducir al máximo posible el peso para prolongar la vida de la batería. Para ello, en 2010 se lanzó al mercado una nueva tecnología de “sandwich” denominada inrekor, que integra un núcleo de ARPRO® con revestimientos adheridos y que proporciona un índice peso-resistencia excepcional. Gracias a su resistencia y elasticidad, inrekor es ideal para el chasis de los vehículos, que ha sido tradicionalmente uno de los componentes que supone un mayor porcentaje en el peso del vehículo. Inrekor puede proporcionar por primera vez a los vehículos eléctricos la ligereza que precisan para convertirse en una alternativa de transporte práctica.
La clave para el uso de ARPRO en los componentes estructurales de bajo peso reside por supuesto en convencer a diseñadores, fabricantes y compradores de vehículos de que este material puede proporcionarles los niveles de resistencia, estabilidad y seguridad que precisan. Sin embargo, la rigidez y la resistencia a la flexión de inrekor aumentan exponencialmente en función del grosor del núcleo, lo que despeja cualquier duda al respecto. Además, su capacidad inherente para la integración “inteligente” de funciones (aislamiento, separación, conducción de aire y puntos de montaje integrados) le proporciona la capacidad de desarrollar soluciones rentables y de muy bajo peso con una mínima inversión de capital. El producto final es fácil de fijar; a diferencia de algunos productos con estructura de nido de abeja, puede remacharse, adherirse, soldarse por puntos o sujetarse mediante fijaciones según los requisitos de la aplicación.
La naturaleza isotrópica del núcleo de ARPRO presente en el interior de inrekor permite que la energía de los impactos se disipe rápidamente en todas direcciones. Ciertamente el sector parece convencido, a tenor del número de vehículos eléctricos altamente innovadores dotados de un chasis de inrekor que últimamente se están comercializando.
En una aplicación típica en un vehículo de cuatro plazas, por ejemplo, es posible reducir el peso del chasis de 300 kg a 160 kg, una importante ventaja dado que una reducción de 1 kg en el peso del vehículo puede llegar a ampliar su autonomía de combustible en 3-4 km. (Los cálculos estiman que el uso de esta tecnología en todos los vehículos de gasolina y gasóleo del mundo permitiría ahorrar nada menos que 10.000 millones de litros de combustible al año.)
Una tecnología versátil que se adapta a diversos materiales
La versatilidad de la tecnología de “sandwich” y los avances en los métodos y los productos de adhesión permiten unir al núcleo revestimientos de diversos materiales en función de la aplicación y los requisitos estéticos. Por otro lado, es posible integrar fácilmente cambios con un gasto en mecanizado o una inversión de capital mínimos, ya que en lugar de proceder al mecanizado por CNC de los paneles de sándwich ya acabados, los núcleos se suelen cortar mediante la tecnología de corte con agua y los revestimientos se cortan mediante láser, una ventaja cuando la velocidad es lo esencial, aunque ambos materiales son también adecuados para las técnicas tradicionales de prensado o estampado. Tenemos un reciente ejemplo en la creación de un depósito de combustible especialmente diseñado para Aston Martin Racing, que dispone de un armazón de inrekor que no solo garantiza un encaje perfecto en la estructura antivuelco del vehículo, sino que además cumple los requisitos de la FIA, que exige que el armazón tenga un grosor de 10 mm. Además, la velocidad a la que es posible fabricar las piezas partiendo de cero queda demostrada por el período de desarrollo de tan solo 13 semanas desde el diseño inicial mediante CAD al uso en el vehículo para un chasis de inrekor completamente nuevo destinado a una reproducción de un Speedster 356.
La versatilidad global de los materiales de bajo peso cobra mayor importancia dada la diferencia en el peso del chasis existente entre las diferentes gamas de modelos, en donde es posible especificar diversas densidades de núcleo en función del peso de cada modelo de la gama.
Gracias a su versatilidad y a su bajo peso, los modernos productos ligeros y las tecnologías de sándwich tales como el polipropileno expandido e inrekor ocupan una posición privilegiada para alcanzar mayores reducciones de peso en numerosas aplicaciones en la actualidad y durante muchos años más.