Piñones en lugar de correas
Gravera recorta costes y reduce gastos de mantenimiento mediante la utilización de motores engranados. En muchos cascajales, plantas de trituramiento de piedras y operaciones similares, la fuerza motora para las cintas transportadoras es proporcionada mediante transmisiones de eje y correa. Esta era también la situación hasta hace poco tiempo en la planta de gravilla de NorStone AS en Tau, emplazada en la región suroeste de Noruega. Recientemente NorStone, una subsidiaria de HeidelbergCement AG, decidió hacer el cambio a motores engranados robustos. Esta opción prometía menores costes de inversión y mayor fiabilidad operacional, así como mayor seguridad en el proceso. También se esperaba una reducción en el consumo de energía gracias a una mayor eficiencia.
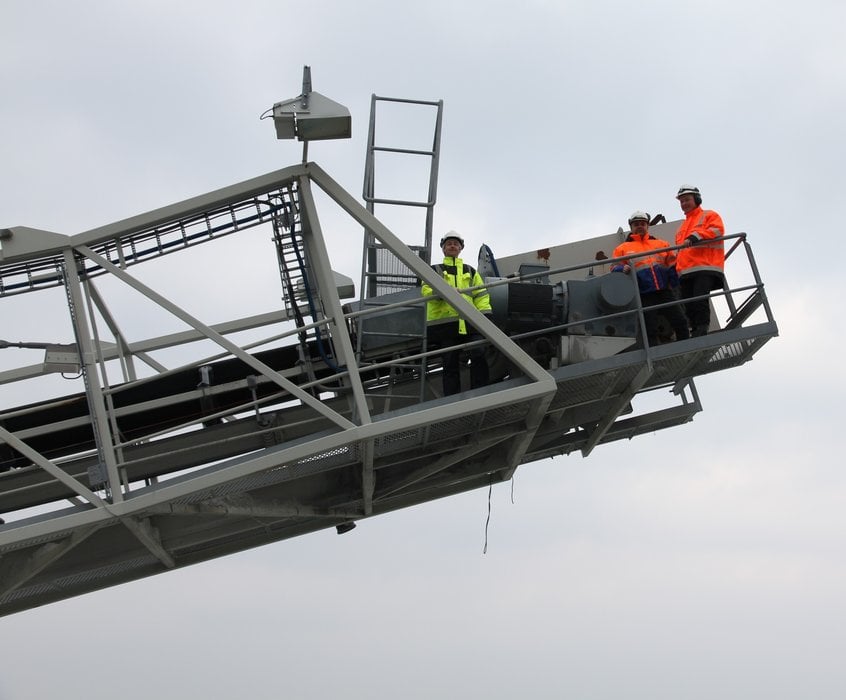
NorStone es el mayor productor de Noruega de productos de gravilla. La empresa proporciona agregados para cemento y asfalto, cubiertas de gravilla para conductos para regiones costeras y otros productos especiales. Cada año las instalaciones productoras de NorStone producen más de 6.6 millones de toneladas de productos de gravilla de varios tipos y rangos de calidad. La demanda es amplia e, incluso con su capacidad productiva anual actual de 2.3 millones de toneladas de material, la planta de Tau apenas puede cubrir la demanda. Esto hace que sea especialmente importante asegurar que la planta permanece operacional el mayor tiempo posible y minimizar el tiempo de parada no programado.
Ventajas conocidas y fiabilidad mejorada mediante transmisiones directas
Los motores engranados no son una novedad en las graveras. Las transmisiones directas de este tipo eran utilizadas de manera habitual en los años ochenta, pero en los años posteriores muchas plantas pasaron a utilizar transmisiones de correas porque los recambios para éstas siempre estaban rápidamente disponibles, mientras que los fabricantes y suministradores de motores engranados no eran capaces de ofrecer provisiones de recambios con la misma disponibilidad. "Nos hemos dado cuenta de que el mantenimiento y los recambios para motores engranados están disponibles para nosotros rápidamente ahora. Mantenemos algunos recambios en almacén nosotros mismos, y para el resto confiamos completamente en NORD Drivesystems como proveedor", explicó Ivar Ullestad, director de mantenimiento en Tau, como la razón para retornar a la solución original. "Esto permite explotar las ventajas conocidas de las soluciones de transmisión mediante motores engranados. En particular, la transmisión directa conduce a una mayor fiabilidad, lo que significa un menor tiempo de parada y por tanto menor tiempo de pérdida de producción. Otro aspecto importante es que se necesita un menor mantenimiento. Además de reducir costes de mantenimiento, esto también aumenta la seguridad en la planta", añadió Ullestad.
Menor desgaste mensurable que con ejes y correas
Las condiciones de trabajo son un factor significativo en estas consideraciones. "Has de tener en mente que trabajamos en el exterior durante todo el año. La mayor parte de las localizaciones para las transmisiones de transporte por cinta son abiertas y sin protección. Debido a las crudas condiciones meteorológicas en el oeste de Noruega, con viento, lluvia y aguanieve, así como el entorno polvoriento y desagradable de la instalación, tratamos de minimizar los tiempos de reparación y mantenimiento para nuestra plantilla de mantenimiento". La planta de Tau funciona siete días a la semana, 24 horas al día en turnos. Las 168 horas de producción incluyen 16 horas de mantenimiento programado. La planta sólo se cierra durante la pausa invernal. Durante esta pausa, se llevan a cabo las tareas anuales de inspección y puesta a punto en dos o tres semanas. Las transmisiones directas han contribuido a aumentar la fiabilidad, suponiendo aproximadamente el 4.5%, en los últimos tres años. "Estamos muy satisfechos con esta tendencia. Con el cambio de transmisiones de eje y correas a la transmisión directa mediante motores engranados de NORD Drivesystems, en primer lugar eliminamos el aspecto del desgaste de la correa, que es considerable. Además, ni agua ni polvo pueden penetrar el mecanismo del motor. Esto significa que la decisión a favor de unidades engranadas compactas y robustas reporta claras ventajas y se ha probado, por tanto, como un movimiento inteligente", resumió Per Thu, Jefe de producción de la planta NorStone. Los motores directos han aportado más que sólo una mayor fiabilidad y una reducción de los gastos financieros y de mano de obra en actividades de mantenimiento. Los costes relativos de inversión al adquirir nuevas unidades engranadas también se han probado menores. Reemplazar un paquete completo consistente de una unidad de tipo árbol junto con poleas de correa, correas, carcasa, protector de correa y motor, resultaron ser más costosos que la compra de un motor engranado comparable. Como una serie de sustituciones de unidades engranadas estaba en cualquier caso programada, un cambio exhaustivo de motores de eje y correa a motores directos era una elección lógica para Ullestad. En este momento está trabajando para estandarizar los componentes del motor. "Con una reducción planificada en los sistemas de accionamiento para las cintas transportadoras, estamos estandarizando aspectos como el tamaño del motor, el tamaño del eje y el diámetro del tambor para limitar la diversidad y por tanto simplificar el mantenimiento, el control de almacén y el servicio. También estamos desarrollando soluciones de resguardo, las cuales implican mantener componentes en almacén nosotros mismos", de acuerdo con el Jefe de mantenimiento.
NorStone AS
La compañía noruega NorStone AS (http://www.norstone.no) es una subsidiaria propiedad de HeidelbergCement AG, uno de los mayores productores mundiales de materiales de construcción como cemento, arena y gravilla. La planta de Tau supervisa, mezcla, controla y proporciona agregados de alta calidad para hormigón y asfalto, así como materiales asfálticos de base con calidad consistente en varias gamas. Los materiales son divididos y cortados en tamaños regulados, tras lo cual son mezclados para obtener curvas de distribución de determinados tamaños que cumplen los requerimientos específicos del cliente. En este proceso, la adherencia a los estándares europeos es monitorizada por laboratorios internos. Entre otras cosas, NorStone proporciona balasto para la industria del ferrocarril, materiales de construcción de carreteras, y materiales asfálticos de base para regiones costeras. La planta de Tau produce 2.3 toneladas de material cada año, de lo que el 75% es exportado.
Figura 1: Planta NorStone
Figuras 2 & 3: La planta NorStone solía tener muchas cintas de excavación como la mostrada en la figura de la izquierda, con un accionamiento de eje y correa conectado a dos motores de 55 kW. Por el contrario, las correas renovadas están equipadas con motores engranados, como la combinación de la unidad SK 9086.1 y el motor de 90 kW mostrado en la figura de la derecha.
Figura 4: La planta de Tau está emplazada junto al océano y tiene su propio malecón, el cual recibe entre 700 y 900 barcos cada año. La cinta de carga está equipada con un motor de 37 kW y una unidad engranada SK 9082.1-225S/4.
Figura 5: Condiciones extremas y especialmente polvorientas: un motor de 15 kW con una unidad engranada SK9052.1-160L/4 ubicada bajo los machacadores de la cinta 10.