www.mexicoindustrial.net
30
'23
Written on Modified on
Rockwell: El sistema AGV centralizado ahorra energía y mejora las operaciones en Michelin
Reducir las emisiones de CO2, mejorar la seguridad, aumentar la eficiencia de la producción y reducir los costes ya no es solo un sueño: ¡es una realidad.
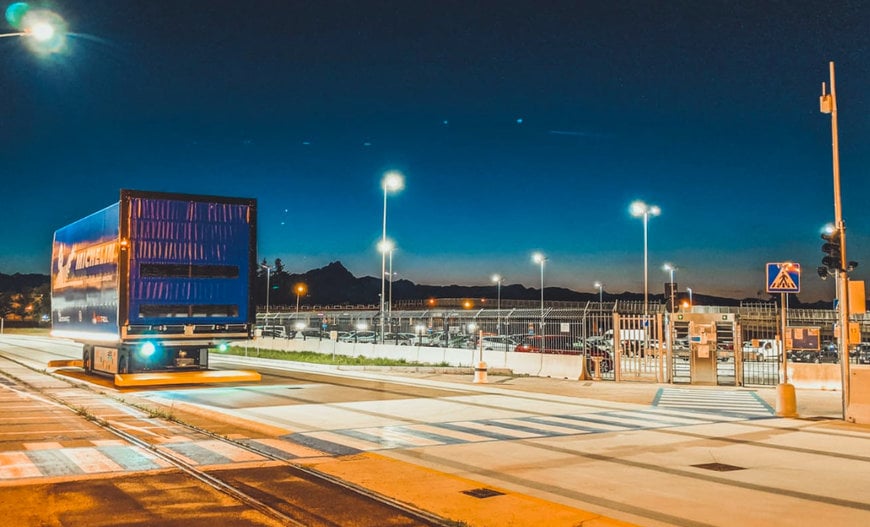
De día o de noche, llueva o nieve, los vehículos de transbordo de la planta de Michelin en Cuneo vienen y van sin parar. Estos seis vehículos de guiado automático (AGV), cada uno del tamaño de un camión y equipados con motores eléctricos, viajan sin parar, las 24 horas del día, todos los días, y recorren los 1500 metros que separan el área de producción y el almacén. Siguen las instrucciones de carga y descarga que se emiten directamente desde el sistema de supervisión de nivel 2 de Rockwell Automation.
Parecen una reproducción a escala de los coches a control remoto de un niño, fascinan a cualquiera que camine por el paso elevado que da a la planta. Sin embargo, no son un juguete gigante, sino que representan un proyecto innovador que no tiene punto de comparación en ninguna otra parte del planeta. Con la colaboración de Rockwell Automation, Giordano & C. ha creado estos vehículos a pedido de Michelin. Representan además un ejemplo de excelencia en el uso de las tecnologías más avanzadas, en apoyo de la transformación digital y la Cuarta revolución industrial.
Su desarrollo e implementación ha permitido que Michelin obtenga importantes beneficios en términos de sostenibilidad, seguridad, eficiencia y, por último, pero no por ello menos importante, costes operativos. El proyecto ofrece una alta capacidad de personalización y, por lo tanto, se puede adaptar a cualquier empresa que necesite procesar grandes cargas al aire libre. Este proyecto ha generado mucho interés en torno a su duplicación en otros centros de producción de Michelin y su implementación en importantes empresas industriales italianas que operan en diferentes sectores, como alimentos y bebidas y farmacéutico, ya se está evaluando.
Como suele suceder en estos casos, todo comenzó con una necesidad específica que expresó el cliente. Michelin, empresa que siempre se ha caracterizado por un fuerte compromiso con la innovación y un excelente modelo de fábrica, quería optimizar el sistema de transporte y la carga y descarga de productos terminados en su planta de Cuneo.
Este cambio implicaba la implementación de un nuevo sistema de manipulación de carga que reemplazaría los camiones utilizados para transferir neumáticos desde el final del área de producción al centro de logística, así como una solución de reemplazo para el elevador de horquilla operado por conductor que ingresaba y salía físicamente de la caja del camión en cada operación de carga y descarga.
Sin posibilidad alguna de utilizar los sistemas de manipulación tradicionales debido a la configuración de la planta, Michelin les pidió a varios proveedores que propusieran soluciones alternativas. El requisito de operar al aire libre y cubrir una distancia de 1500 metros añadió complejidad incluso para los proveedores con más experiencia. Por todo ello, era esencial pensar de forma independiente y aplicar el mismo método adoptado en las plantas que se desarrollan en terrenos industriales abandonados donde se comienza con lo que está disponible y se aprovecha al máximo todo lo existente.
Así fue exactamente como Giordano & C., empresa italiana fundada en 1924 y hoy reconocida integradora de sistemas con presencia internacional, asumió el reto. La tarea por realizar no era fácil, pero no se dejó intimidar por los trabajos de construcción necesarios para crear una infraestructura de transbordo para los vehículos; además, involucró en el proyecto a Esatroll para la provisión de vehículos con características específicas.
Más adelante en el proyecto, Giordano & C. recurrió a Rockwell Automation, una empresa con la que ha trabajado durante mucho tiempo, respaldada por el hecho de que es un socio OEM nivel Gold de Rockwell Automation. A fin de poder controlar los vehículos de transbordo, fue crucial integrar el sistema AGV con el sistema de comunicación de nivel 2 que Rockwell Automation utiliza como estándar en las plantas de Michelin.
A primera vista, esta solución se puede interpretar como una simple externalización de la logística de almacén gestionada a través del sistema AGV. Sin embargo, en realidad existen algunas peculiaridades que no se suelen encontrar en otros proyectos similares. En primer lugar, la gran distancia entre las áreas de producción y el centro de logística implicaba importantes trabajos de construcción. A diferencia de un sistema AGV diseñado para su uso en interiores, estos vehículos de transbordo tienen características mecánicas que los hacen similares a cualquier camión que circula por la carretera y, por lo tanto, están equipados con ejes, ruedas, chasis, etc.
Otro elemento de diferenciación está dado por el software, ya que estos vehículos incluyen un sistema de navegación que les permite operar bajo cualquier tipo de condición climática. Además, el sistema de control de navegación se conecta a través de la red de comunicación de nivel 2 de Rockwell Automation, lo que significa que los vehículos de transbordo funcionan de acuerdo con las órdenes que reciben directamente del sistema central. Todos los paneles de control de los muelles de carga y descarga, así como todas las interfaces entre el sistema de nivel 2 de la planta y la flota, se gestionan mediante soluciones de tecnología de Rockwell Automation, lo que permite la conexión entre las áreas de producción y transporte de la fábrica.
Una vez finalizada la producción, el sistema de nivel 2 comunica que hay material listo para la carga en el muelle al final del área de producción y para su descarga en otro muelle específico del polo logístico. Todas estas operaciones se realizan según las reglas que haya especificado el cliente, las que Giordano & C. se encarga de integrar en el sistema de navegación. Una vez que se completa la operación, se envía la información al sistema de nivel 2, a fin de que Michelin conozca al detalle la cantidad de pallets en existencia.
Mediante el uso de tecnologías digitales avanzadas, Michelin ha logrado reducir las emisiones anuales de CO2 en 50 toneladas y, en concreto, la elección de emplear vehículos de transbordo con motores eléctricos, cuyas baterías se recargan durante las fases de carga y descarga, ha permitido alcanzar el objetivo de cero emisiones. Otra característica de interés es el aumento global de la seguridad en el lugar de trabajo, también desde el punto de vista de las comunicaciones.
La tecnología de gateway inalámbrica que proporciona ProSoft Technology, un socio de tecnología nivel Silver de Rockwell Automation, permite una transferencia fácil y segura de información entre la flota y el sistema de nivel 2, a través del protocolo de seguridad CIP. La velocidad a la que se puede intercambiar información de producción y logística resulta igual de interesante. Esta capacidad se logra gracias a un procesamiento en tiempo real y a la comunicación con el sistema de nivel 2 de Rockwell Automation, que le permite a Michelin tener una visión integral de los materiales de producción y en existencia en todo momento.
www.rockwellautomation.com